Deployment of solar PV is attaining incredible momentum as the cheapest clean replacement of fossil fuel electricity generation, and production of silicon solar cells is at such a scale that to change manufacture of the dominant technology (PERC), or reconsider investment in emerging technologies (for example, heterojunction solar cells) is like turning an ocean liner.
But a new research paper — a data-driven, number crunching exposé — from scientists at the University of New South Wales’ renowned School of Photovoltaic Renewable Energy and Engineering (SPREE) shows that to meet projected solar generation requirements of some 70 terawatts of solar PV by 2050, the industry must urgently steer towards technologies that use less silver, bismuth and indium, if they don’t want to overwhelm the earth’s supply of these materials and be left high, dry — and unexpectedly expensive.
Industry expert, Adjunct Professor Pierre Verlinden, has been sounding the siren of material scarcity in PV for years; Associate Professor Brett Hallam, a brilliant SPREE researcher working on how to increase the efficiency of solar cells was becoming worried about the sustainability of upcoming solutions to boosting efficiency; and Yuchao Zhang had begun his PhD research around the metallisation and screen printing used in solar cells when Verlinden and Hallam suggested he look at sustainability first.
The combined SPREE of knowledge
“We did some quick calculations that showed, OK, there is definitely a problem for the future consumption of silver, bismuth and indium,” Zhang tells pv magazine Australia.
A team of five co-authors formed to look into global reserves of these resources, and they drew on the combined expertise of SPREE to calculate how much of each material is currently being used in dominant and emerging technologies, and how much will be required for future PV production.
“Then, from a more technical perspective, we looked at the impact on cell performance of reducing the use of these substances, and how far we could reduce the usage in different solar cell technologies,” says Zhang, without sacrificing hard-earned efficiency gains made over the past decade.
The upshot of the paper — Design Considerations for Multi-terawatt Scale Manufacturing of Existing and Future Photovoltaic Technologies: Challenges and Opportunities Related to Silver, Indium and Bismuth Consumption — published today in the journal Energy & Environmental Science, is that the industry and academics must temporarily put aside the pursuit of greater solar cell efficiency and instead focus their abilities on primarily reducing the use of silver in PV.
Possible efficiency gains from new technologies cannot yet neutralise the draining of silver, bismuth and indium reserves as manufacturers ramp up PV capacity to respond to demand for clean energy at a scale that will significantly impact climate change.
The Design Considerations paper takes as its basis that PV module production must increase from 135 GW in 2020 to 3 TW by 2030.
It assumes an upper material consumption limit of 20% of 2019 global supply of the three most constrained materials, given that other industries also have a claim to those reserves.
The hard edges of silver reserves
As such, its authors calculate that the present industrial implementation of passivated emitter and rear cell (PERC) has a sustainable manufacturing capacity of 377 GW (limited by silver supply), tunnel oxide passivated contact (TOPCon) has a capacity of 227 GW (limited by silver supply) and silicon heterojunction (SHJ) has a capacity of 37 GW (limited by indium supply).
To cut the finite cake a different way, the paper says, that to enable a 3 TW market, silver consumption alone must be reduced to less than 2 milligrams per watt (mg/W) of generation.
The current consumption of silver for industrial PERC solar cells is approximately 15.4 mg/W, while that for TOPCon and SHJ solar cells is approximately double at 25.6 mg/W and 33.9 mg/W, respectively, due to the reliance on silver on both the front and rear contacts,” the researchers reveal.
Despite the fact that the International Technology Roadmap for PV (ITRPV) predicts a 50-60% reduction in silver used for each of these mainstream technologies over the coming decade, it still calculates expected consumption in 2031 of 8.5 mg/W for PERC, 13.8 mg/W for TOPCon and 14.3 mg/W for SHJ.
Why sustainability temporarily trumps efficiency
In an exclusive interview, Hallam told pv magazine Australia that assuming PERC has an efficiency ceiling of 24-25%; and TOPCon and SHJ offer only a tiny gain to 25-26%, it would make more sense to continue scaling PERC production in anticipation of then switching to tandem solar cell production, because tandem cells have the known potential for 30% efficiency, which will itself allow reduced use of critical materials for the same required generation capacity.
But the UNSW team is concerned that manufacturers are investing heavily in SHJ cell production, which will suck up the most silver for not much additional benefit.
Hallam estimates that manufacturers are investing in some 40-50 GW of heterojunction manufacturing, which he calculates, would also “potentially use up to 60% of global indium supply”.
Indium is produced exclusively as a byproduct of processing other metal ores such as zinc, and more than 70% of supply is directed toward production of indium tin oxide (ITO), which is much in demand for its conductive yet transparent properties when applied as a film in touchscreens, flat-screen displays, glass windows, and PV cells.
Using less ITO in PV cells — films of, say, 20 nanometre thickness compared to 100 nanometre thickness, combined with an indium-free layer — would only enable around 200 GW of SHJ manufacturing, but would not support production at terawatt scale.
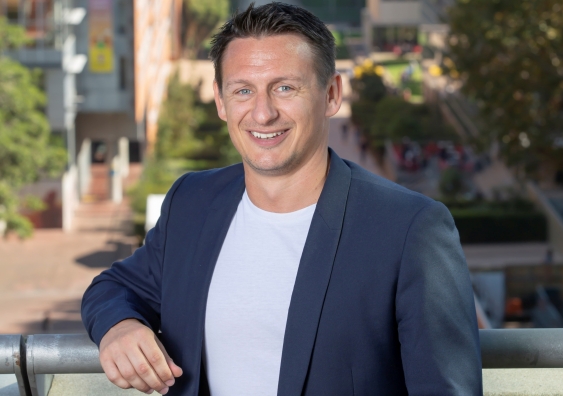
Image: UNSW
Why tandems are a future standout
“One of the really exciting opportunities for tandems if they’re two-terminal,” says Hallam, “is that the current is halved and the voltage is tripled compared to PERC; and the reduced series resistance losses mean we can potentially reduce silver consumption by a factor of six.”
Hallam says reviewers of the paper before its publication were shocked by the numbers obtained for tandem use, and at least one had gone back over the calculations to verify them. “They came back to confirm we were completely right,” he says.
The discovery “means we can maintain the multi-busbar technology and silver fingers as we use them now, while massively reducing the requirement for silver”, he says.
The Design Considerations paper also urges researchers and manufacturers to accelerate innovation in screen printing technologies for PERC, TOPCon and SHJ solar cells, to reduce silver consumption beyond the expectations of the ITRPV, or to move widespread adoption of proven copper plating technologies (see Pierre Verlinden Q&A for more on the changing constraints on copper plating).
Why bismuth is not the cool answer to every hot issue
Bismuth, the least abundant of the three materials identified by UNSW as “endangered” by PV production, is currently the go-to material used in alloys for cool soldering of heat-sensitive SHJ cells. But it is also considered a promising low-temperature alternative to lead-based solders used in PERC and TOPCon technologies.
The paper identifies that 20% of 2019 global bismuth supply would enable less than 300 GW of production with today’s bismuth-based interconnection technologies — so there’s an urgent case for “investigating the use of tin-bismuth coatings with substantially lower bismuth contents, or alternatively the use of electrically conductive adhesives”.
The circular economy won’t spin fast enough
The SPREE team looked briefly at the potential for harvesting the three scarce materials from recycled solar cells, but the 25-year lifetime of solar infrastructure means that supplies of recovered materials will not reach levels to support terawatt scale production for decades — and that’s assuming that recycling technologies can be developed to efficiently recover not only glass and aluminium from solar panels, but access the potential riches of silver in particular.
The rising value of ever more scarce silver, indium and bismuth may accelerate development of such processes.
Tough love?
The research carried out by UNSW might be considered a blow to proponents of some PV technologies, but on the whole it should help focus industry development and investment in manufacturing towards sustainable options.
For example, says Hallam, it shows that “If we stick to the path of screen printing with silver fingers, then we should be manufacturing PERC until we switch to tandem. We can only consider TOPCon and heterojunction if they offer lower silver consumption, and don’t introduce new critical challenges like indium and bismuth”, a finding that encourages development of plating.
Hallam concedes that he was worried about the reception the paper might receive, but in fact he says it’s received “the most positive reviews I’ve ever had on a publication and probably ever will have”.
He says reviewers have generally highlighted the importance of the UNSW paper for the industry.
Zhang adds it’s vital that manufacturers look to the future: “With something like a tenfold increase in annual production capacity, material consumption is definitely going to be a concern.”
He says companies may already have spent millions or billions of dollars on building their production lines, “and this kind of risk is not something they will be happy to see, but I would expect this paper to at least raise some awareness in the industry and give them the incentive to look into more efficient ways to use these materials”.
This content is protected by copyright and may not be reused. If you want to cooperate with us and would like to reuse some of our content, please contact: editors@pv-magazine.com.
2 comments
By submitting this form you agree to pv magazine using your data for the purposes of publishing your comment.
Your personal data will only be disclosed or otherwise transmitted to third parties for the purposes of spam filtering or if this is necessary for technical maintenance of the website. Any other transfer to third parties will not take place unless this is justified on the basis of applicable data protection regulations or if pv magazine is legally obliged to do so.
You may revoke this consent at any time with effect for the future, in which case your personal data will be deleted immediately. Otherwise, your data will be deleted if pv magazine has processed your request or the purpose of data storage is fulfilled.
Further information on data privacy can be found in our Data Protection Policy.