In May, Australia’s Minister for Climate Change and Energy, Chris Bowen, told an audience in Sydney that a lack of labour and social licence could both slow Australia’s renewable energy transition, but issues in supply chains, “could actually stop us.”
Utility-scale renewable energy projects are suffering delays in Australia at the moment – some of these stem from an inability to source equipment, including central inverters and the integrated “power stations” they are increasingly packaged into. Given variations of inverter equipment sits across every renewable energy project, be it solar farms, wind, or battery storage, disruptions have major ramifications. Grid connection, labour shortages, the growing cost of capital, high inflation, land approval disputes and booming global demand are also major factors in project delays.
Lead times for central inverters and power stations used to average around six months. Today, Australia’s top utility-scale manufacturer, German company SMA, is reporting 12 months; Spain’s Ingeteam, second in the leaderboard, looks to have a similar timeframe. Meanwhile, Chinese brand Solis has had to delay the launch of its utility-scale inverter products in Australia.
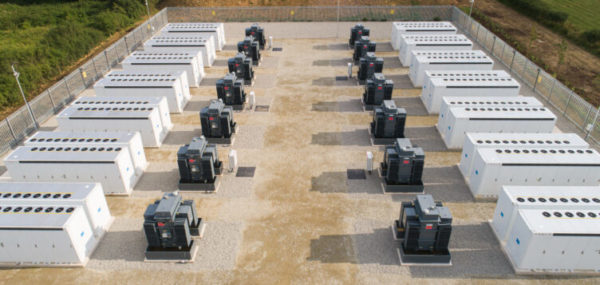
Image: FRV
It is not alone – Ingeteam launched a new central inverter product model in late 2022, but doesn’t expect Australia to house any of these until well into 2024. Both companies have pointed to difficulties sourcing enough components as a key cause of the stall, though other factors are also at play which will be discussed shortly.
This is a key point though: the issue here is not manufacturing inverters themselves, but rather stems from the lack of critical components, most notably transformers, which go into inverter power system products.
“Many critical components have very long lead times,” Carlos Lezana Visus, Ingeteam’s Global Marketing Manager, told pv magazine Australia. These issues have led the company to modify its processes, introducing special new processes to accommodate longer lead times for components.
SMA’s Large Scale and Projects Solutions Manager, Josh Birmingham, also noted a number of these components including clips, switches, and the steel inside transformers, are also in demand by the rapidly growing electric vehicle (EV) industry, leading to further shortages.
Unlike Australia’s top players in the space, Chinese brand Sungrow, a newcomer to the utility-scale inverter segment, reports lead times of six months for Power Conversion Systems for big battery projects and even less for solar projects, Henry Liu, Sungrow Australia’s Grid Connection and Product Manager, told pv magazine Australia. Liu pointed to the company’s vertical integration, noting it produces critical components and sub-assemblies, as a reasons for its shorter lead times. Liu also noted the company’s global manufacturing footprint, which he says has allowed Sungrow to minimise transportation and logistical complexities,.
It is also likely that, because Sungrow is new in the segment, there is less demand for its products compared to brands like SMA and Ingeteam.
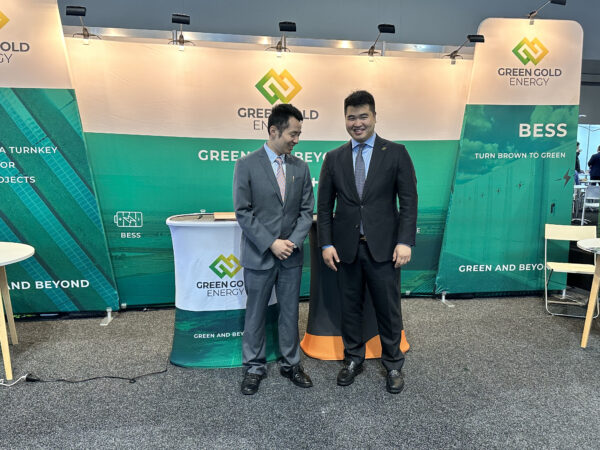
Image: pv magazine
SMA & the push for local manufacturing
SMA is currently in the process of doubling its production capacity in Niestetal, Germany – growing from around 20 GW per annum to 40 GW. Birmingham told pv magazine Australia the company is going to have to double this again to keep up with demand which is mushrooming in Europe and the US.
Birmingham thinks that given Australia is vying with much larger countries, often with more generous renewable support programs, Australian governments need to be doing more to secure its supplies of equipment.
Energy Minister Chris Bowen has frequently echoed this thought, telling Sydney audiences at the Smart Energy Conference in May that it is “inconceivable” just 1% of the 60 million solar panels installed in Australia were actually manufactured onshore. “Same goes with all the other elements in the renewable energy supply chain,” Bowen said. “We need to be making more things here.”
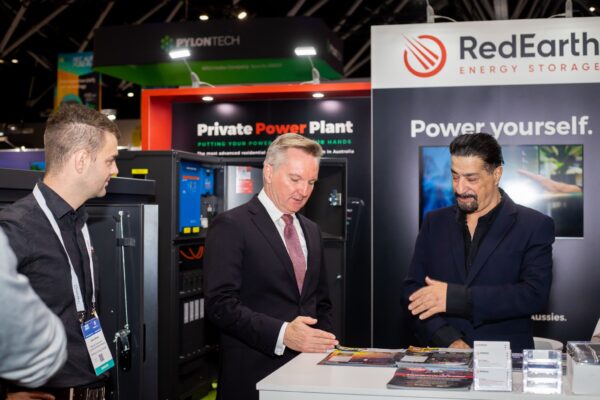
Image: RedEarth
Clean energy supply chains and manufacturing is now the main issue addressed at energy minister “quad” meetings, Bowen said. “We manly focus, almost exclusively, on supply chain and what we can do to get each other making more things.”
Despite not being a particularly new proposition, little clean energy manufacturing has eventuated to date. Manufacturing onshore is often cast as a pipe dream by critics, who point to Australia’s high labour prices.
Given that labour costs account for much less than 5% of SMA’s total production costs, Birmingham doesn’t consider this a major hurdle. Australia is still definitely a viable location to produce inverters in his eyes. “If conditions were right, we [SMA] would open a factory in Australia.”
By conditions, Birmingham is pointing to government support in the form of guaranteed demand. For manufacturing to be worthwhile, government needs to help guarantee the market by, for instance, introducing and strictly enforcing local content requirements, Birmingham says.
Ingeteam benefits from Australia’s particularly lengthy grid connection process
While usually bemoaned as the root of delays and lost capital, Ingeteam’s Carlos Visus said Australia’s strict grid connection processes offered it a welcome buffer.
The Australian Energy Market Operator’s (AEMO) Generator Performance Standards, or GPS process, usually takes around one year or more to complete. (CEO Daniel Westerman yesterday insisted AEMO was connecting projects “as quickly as we can,” but Spanish Visus pointed out the uniqueness of the Australian process, which he noted was “not happening in most of the rest of the world.”)
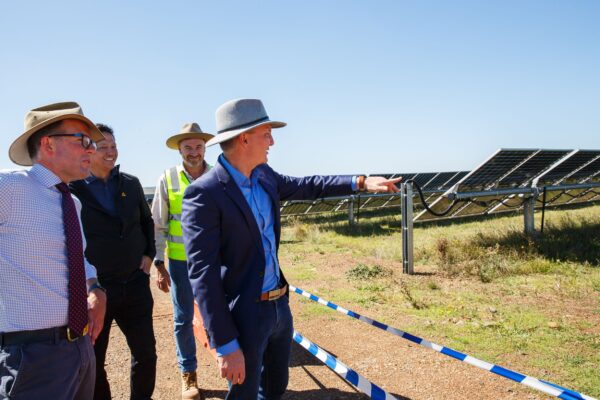
Image: ACEN Australia
While Ingeteam is rarely formally awarded project contracts before developers begin the GPS process, Visus said that in reality the company can move with confidence knowing the process is modelling its product. “No developer would dare to change the technology after all these tests had been approved.”
“So we can start planning all this supply chain to get all the components we need to manufacture the number of inverters we need for that specific project with a lot of advance,” Visus said. “That is why we can have improved logistics in terms of Australian projects. Maybe in other countries, it is harder for us because we have less time. But in Australia we know there is going to be one year, one year and a half, maybe two years even, between when the grid studies starts until when they finish.”
“Otherwise it would be a very different situation and we would be talking about probably problems trying to supply all that we need to supply on time,” he added. “The grid status, in this case, it is good news for us.”
Ingeteam has installed or been awarded nearly 3.5 GW of projects in Australia today. As mentioned, the company launched a new central inverter product model in late 2022 – which, while offering improvements, is a more onerous model to manufacture in terms of componentry.
This, plus the fact Australia’s grid processes take so long, means Ingeteam will continue to favour the older model here, using it on all projects throughout 2023. It is already running grid status processes with AEMO for new model but will wait until this is fully completed before offering the model in Australia.
“We need to wait until all this grid studies are done and are successfully passed to start to manufacture and supply all these new inverter models for Australia,” Visus said, pointing to a start date maybe by 2024.
Factors collide and compound
To understand the Australian market’s lead time blow outs, the global picture warrants consideration. Europe is trying to decouple from Russian gas by ramping up renewables, the US has introduced the one of the globe’s largest renewable subsidy programs in its Inflation Reduction Act, meanwhile skyrocketing energy prices have seen the residential and commercial segments surge.
Given the free market dictates that product flows where the most money is, the substantially larger markets of Europe, the US, and Asia, including China and India, simply have greater pull than Australia.
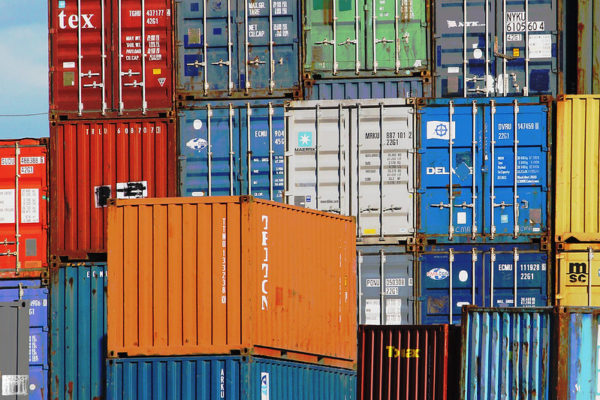
Image: jan buchholtz/Flickr
Both within and outside of Australia, the renewable energy industry is in something of a “frenzy,” as Risen Australia’s Grid Connection and Technical Services Manager, Michael Forder, puts it. Projects put on pause during Covid have restarted, and new government targets and policies have kicked the industry into a new gear.
Meanwhile, disruptions from the pandemic continue to reverberate. “What we’ve found is main power transformers, inverters, circuit breakers, isolators and disconnectors – two years ago, I started seeing general lead times increase 20-50% and even in some instances to 100% so that 20 weeks become 30 become 40,” Forder told pv magazine Australia.
“It was fundamental resource shortages: the factories had people with Covid, so they couldn’t do their three shifts a day; their raw products were being constrained, they couldn’t get the raw products in; the shipping delays due to lack of shipping containers, lack of ships, all sorts of other reasons there. So things started to take longer to be delivered and cost more.”
“I don’t think inverters are anything special – they’re just caught up in the general issues,” Forder added.
This content is protected by copyright and may not be reused. If you want to cooperate with us and would like to reuse some of our content, please contact: editors@pv-magazine.com.
By submitting this form you agree to pv magazine using your data for the purposes of publishing your comment.
Your personal data will only be disclosed or otherwise transmitted to third parties for the purposes of spam filtering or if this is necessary for technical maintenance of the website. Any other transfer to third parties will not take place unless this is justified on the basis of applicable data protection regulations or if pv magazine is legally obliged to do so.
You may revoke this consent at any time with effect for the future, in which case your personal data will be deleted immediately. Otherwise, your data will be deleted if pv magazine has processed your request or the purpose of data storage is fulfilled.
Further information on data privacy can be found in our Data Protection Policy.