From the December edition of pv magazine
Tortured metal, modules lying face down in pools of muddy water, tracker rows twisted like denatured strands of DNA: The sight greeting engineering crews on Oct. 18, 2018, at the Oakey 2 project is the stuff of solar-engineering nightmares. And unfortunately, it’s not a unique case.
The 55 MW Oakey 2 project is located in the Darling Downs region in southeast Queensland, Australia. As the name implies, it is the second stage of the larger Oakey Solar Farm – its sister project, the 25 MW Oakey 1 array, began power production in March.
Canadian Solar snapped up Oakey as a part of its acquisition of U.S.-based developer Recurrent Energy in 2015. It picked up the portfolio at attractive prices – some $0.07/Wp for the largely U.S. and Australian projects. Australia’s federal agencies provided support to both stages of the utility scale array. Oakey 1 picked up an AUD 2.2 million ($1.5 million) grant from the Australian Renewable Energy Agency (ARENA) – a part of ARENA’s large-scale solar program that effectively kick started the market segment in the country. Clean Energy Finance Corp. (CEFC) provided AUD 19.5 million ($13.2 million) in debt finance towards Oakey 1. It then doubled down, providing AUD 55 million ($37 million) toward Oakey 2.
The Foresight Group, through its Foresight Solar Fund Ltd. investment vehicle, took a 49% share in Oakey 1 and a 100% stake in Oakey 2 in October 2017. ARENA and the CEFC declined to comment or provide any information as to the problems encountered on the second stage of the Oakey project.
The failure
The precise details of the catastrophic event that occurred at Oakey in the Australian spring of 2018 are difficult to ascertain. Few who were involved are willing to discuss the project, which is not entirely surprising, given that litigation is likely to envelop suppliers and stakeholders.
The Queensland Electrical Safety Office has confirmed that the event took place on Oct. 18. A spokesperson confirms that a “severe storm” hit the site, at which construction had been halted due to the risk posed by lightning strikes. Approximately 2,000 Canadian Solar modules were damaged by the event. And the photos present vivid evidence of what went wrong.
Both from the air and neighboring properties, photos show cable trenches full to the brim with muddy brown water. Modules on the top row of the “two-module-in-portrait” tracker structure are twisted off vertically, with some having come completely free. The piles onto which the trackers are mounted are bent, with modules at 90 degrees to the horizon. Some rows have completely collapsed, with steel puncturing modules, and the whole structure resembling little more than a tangled wreckage. And, perhaps most tellingly, badly damaged rows are twisted in a kind of demented helix.
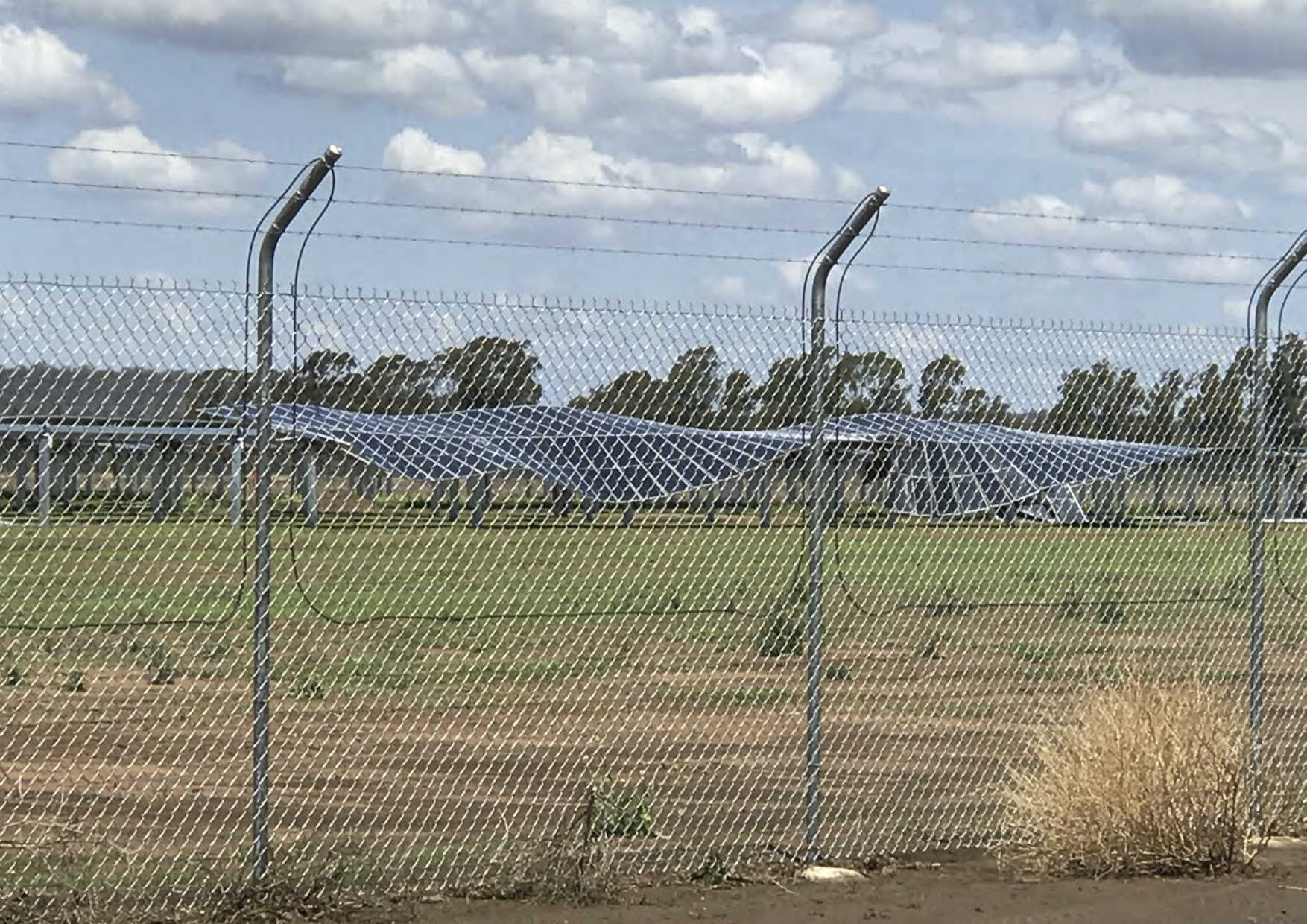
Photo: Supplied on an anonymous basis
“It looks like typical damage from torsional galloping to me,” says Thorsten Kray, the Head of Building Aerodynamics at the I.F.I. – the Aachen-based Institute for Industrial Aerodynamics. “The torque tube appears twisted and it looks like it is most pronounced at the end of rows, which would also be typical – because that is the weakest part [of the row], where the stiffness is lowest.”
Australian Bureau of Meteorology data reveal that top wind gusts at its observation post some 10 km from the Oakey 2 site recorded 46 km/h wind gusts – although local winds as the result of the thunderstorm could very well have been more intense. IFI’s Kray says that such winds are probably causes of the torsional galloping mechanism.
“During thunderstorms the wind picks up quickly until it reaches the critical speed for torsional galloping,” says Kray. “Next, the wind speed keeps on increasing and with it the torsional motion.”
Torsional galloping and the wind resistance of trackers has become a hot PV-industry issue in recent months. It occurs when trackers stow at zero degrees to decrease the wind load on each individual pile or post. But it does introduce torsional motion, even with light winds, says IFI’s Kray. And as the wind picks up, if there are no mechanisms built into the system to restrain the galloping, the event is a runaway disaster.
“At zero degrees, even the static torque is quite high,” explains Kray, referring to the wind action on the tracker row. “In addition, there is instability with [wind] vortices shedding alternately from the leading and trailing edges of the tracker which can lead to increased oscillations and amplitude with each cycle. Once there is an onset of torsional galloping that is characterized by periodic vortex shedding and increasing amplitude, it can’t be stopped unless the wind speed falls significantly below the critical threshold at which it was initiated. With increasing wind speed, it will continue until the tracker swings up to plus or minus 90 degrees … or until total damage happens.”
The picture is a dramatic one. The tracker ends flutter, then begin to twist from the edge in toward the central modules, where the row is at its most rigid, buffered by the drive. This twisting increases in intensity, insidiously spreading from one row to the next. Until the tracker twists itself to pieces.
Tracker stability
In recent months, tracker suppliers have been falling over themselves to demonstrate the wind credentials of their designs. Some have taken active methods to stiffen their structures to reduce the likelihood of torsional galloping occurring, while others rely on shorter rows, increasing the natural frequency of the structure, significantly reducing the likelihood of the “galloping” runaway-failure event.
There has also been increased activity in wind tunnel testing of tracker models before deployment in the field. The methodology in terms of how these tests are being utilized is also becoming more sophisticated, however some claim improvement is still required.
“Not all wind studies are created equal,” says Alex Roedel, the director of design and engineering at Nextracker. “Even the brightest structural engineers in the country will take a wind tunnel test at face value, [but] we have a peer review of that [wind test] and that is extra important.”
Roedel also observes that higher tracker structures with larger modules mounted on them, due to bifacial configurations or even larger wafer sizes, are increasing the importance of wind tunnel testing and system design. “A lot of the modules are getting bigger, and it’s not linear but a squared value and it absolutely it adds to dynamics around wind.”
EPC equation
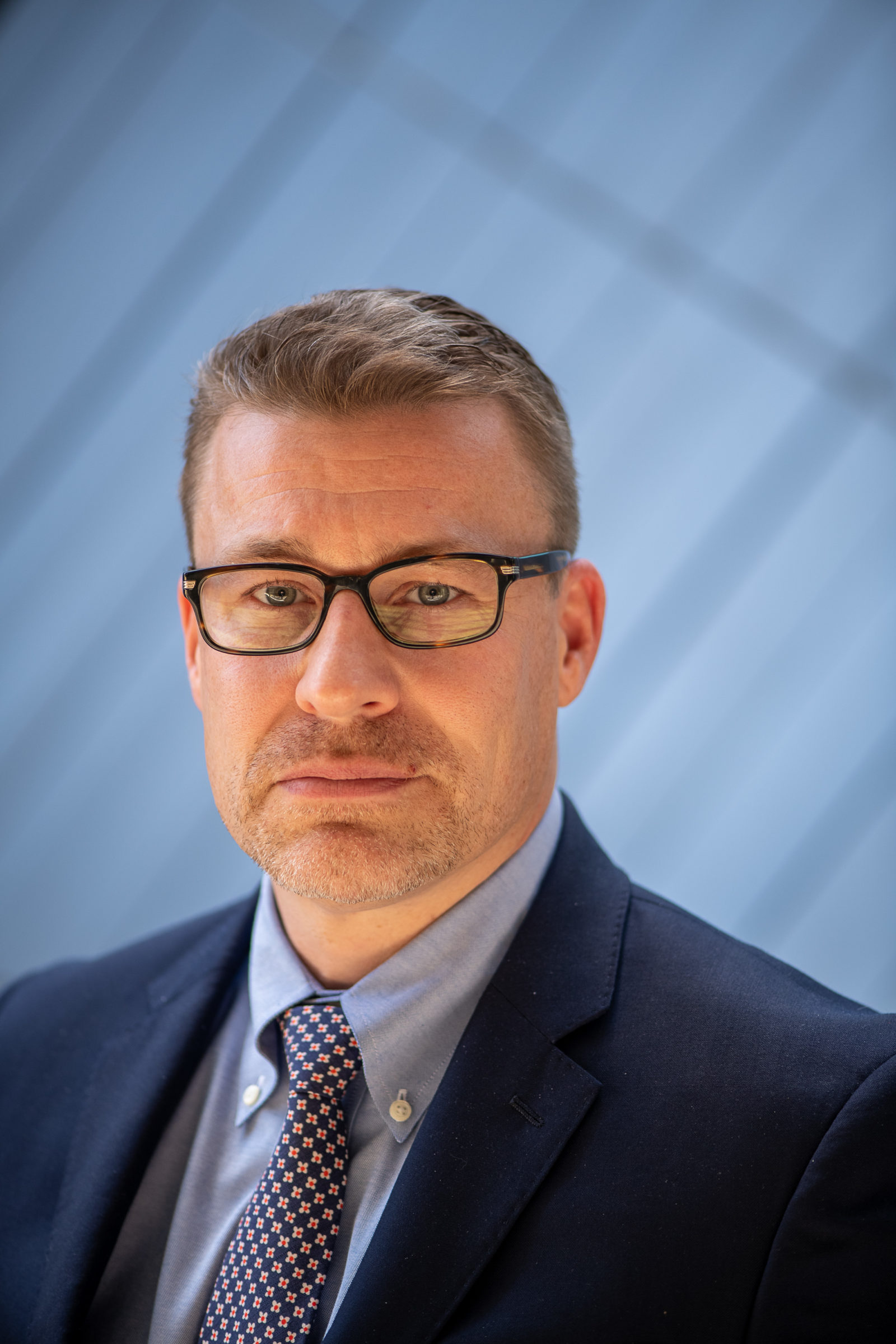
Photo: pv magazine/Dave Tacon
One of the potentially mitigating factors surrounding Oakey 2 is that the site was not fully installed and operational at the time of the failure. Thomas Koerner – Canadian Solar VP of global sales, module and systems solutions – reports that “some of the panels were partially installed [at Oakey 2] when the storm hit.
“The key learning is while you are building a site, you have to expect the unexpected,” Koerner continues. “During construction you have to be prepared for everything, right down to properly cleaning the site of construction materials. The entire construction process must be considered, [in terms of] when you are doing what, how you are securing it, when the trackers should be installed.”
Koerner describes the October 2018 event as “not insignificant” and that it caused “weeks” of delays in project finalization. “We are simply repairing that and bringing the project to completion.” Oakey 2, he claims, is “nearing completion now.” Foresight Group confirms the plant began producing power in the second quarter of this year.
Canadian Solar was acting as the EPC on Oakey 2, however it subcontracted the work to Biosar. Greece-based Biosar completed the construction and achieved full grid connection for the 95 MW Susan River project in Queensland, for Elliot Green Power (EGP). EGP announced that construction had been finalized on the project in February 2019. A spokesperson for EGP would not be drawn on whether the project had met Generator Performance Standards as prescribed by the regulator, the Australian Electricity Market Operator (AEMO).
Australia’s “long and skinny” electricity network is widely understood to be posing considerable challenges for solar EPCs. AEMO is tasked with maintaining grid stability and function during the current period in which renewables are growing quickly, and some old fossil-fuel generators are exiting the market. Meeting GPS, often termed “full grid acceptance,” through the successful completion of R2 testing, is an ongoing sticking point for Oakey 2. While the project was scheduled to be completed, and presumably meet GPS, by the end of 2018, indications are that its final acceptance testing is still some time away.
SMA supplied the power electronics to both stages of the Oakey Solar Farm. “SMA is committed to do all that we can do to make sure these plants are fully compliant and connected to the grid,” says SMA Australia’s Josh Birmingham. “There are still some outstanding questions on grid modeling, and we continue to support Bisoar.”
Long-established Australian engineering and infrastructure firm RCR Tomlinson rapidly collapsed in late 2018, due in no small part to a large number of its solar projects encountering delays in completing R2 testing – and the related penalties that were quickly incurred. RCR had been executing Oakey 1 when the company collapsed, causing some delays. Oakey 1 was left unscathed the previous October, as confirmed by ARENA, while Oakey 2 tore itself to pieces.
Despite Canadian Solar’s optimism, there is every reason to believe that Oakey 2 has been a financial disaster for those involved. It looks highly likely that system design, component selection, pile installation, or a combination of all three were inadequate. There is the suggestion that upon realizing the challenges posed by clearing AEMO’s high GPS bar, corners were cut. Costly litigation is the probable outcome, as the finger of blame is pointed. It’s not all beaches and BBQs under the Australian sun.
This content is protected by copyright and may not be reused. If you want to cooperate with us and would like to reuse some of our content, please contact: editors@pv-magazine.com.
This kind of carnage reminds one of the well known Tacoma Narrows bridge, built in 1940. When the wind through the narrows hit a ‘specific’ velocity, the structure broke into torsional oscillations that ripped the bridge apart. One of the findings was the ‘span’ was too long for the amount of material used to construct the bridge. I can imagine with the right wind loading, the 2P panel mounting began to flex like an airplane wing at takeoff. The wind event must have lasted long enough to flex then fracture the panel mounting points or the actual frames of the panels themselves.
Not all trackers are equal. Same designs produce the same effects. We at Nexans Solar Technologies have developed a disruptive innovative solar tracker that rely on a completely different design. On top of not being sensible to galloping and vortex locking, it stands on 2 posts only simplifying fondations and installation. The tracker is 80% prefabricated and so we can offer unprecedented quality and assembly cadency, no adjustment required. It accept all slopes and is ground settlement compliant.
I worked on this project from almost commencement to almost completion. That storm was very fierce. This site should never of been a site for such installation (known storm area, unpredictable black soil when wet) poorly designed and very weak steel componets and the sub-contractor employed by the EPC left a lot to be desired. There was no dampners attached to the tracker systems, again the components were of serious inferior quality (affixing components). I could go on but the pictures and site investigations will reveal the major fault/s
You are right, now it’s in the courts over in Brisbane https://www.courts.qld.gov.au/__external/CourtsLawList/Brisbane.htm
who is the tracker Supplier??
Very good reason not to use trackers. Apart from the fact they dont justify the expence as any increased production is neglishable.
Peter
This project is now open in dispute in the Queensland Supreme Court in August 2023- no surprises after its bad history with biosar not paying the suppliers
https://www.courts.qld.gov.au/__external/CourtsLawList/Brisbane.htm