From ISSUE 12-2021.
In late October, Japanese thin-film PV producer Solar Frontier announced its decision to pull the plug on its CIGS (copper indium gallium selenide) solar module production facility in Kunitomi, southern Japan. The 800 MW production facility had been inaugurated in 2011 and, at the time, had been the flagship CIGS factory globally – a lodestar for global CIGS producers, demonstrating that the technology could achieve close to gigawatt scale.
Urban Solar
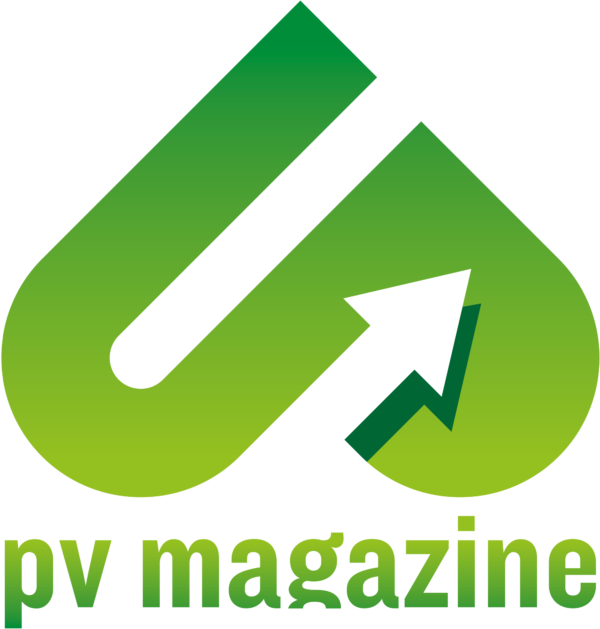
Walking the factory floor when the plant had first been fired up, it was difficult not to marvel at the high levels of automation and intense focus on quality that the Japanese production engineers had deployed at the Kunitomi facility. It was no surprise in subsequent years to learn that the CIGS modules rolling off the production lines exceeded performance expectations when speaking to EPCs and project owners in Europe and the United States.
In the years after the factory’s opening, the strong Japanese domestic PV marketplace delivered sufficient demand to the factory owners, as Showa Shell had invested for decades in the development of Japanese CIGS technology. But as Chinese crystalline silicon (c-Si) rivals made inroads to the Japanese PV marketplace, which had long been skeptical of the quality of Chinese products, Solar Frontier’s CIGS modules could not compete on conversion efficiency or cost.
Module efficiencies for the CIGS modules rolling off the Kunitomi lines reached 15.5% in mass production and, while cost structures were never announced publicly, the opinion of leading PV technology analysts was that they had struggled to come down much below the $0.80/W mark – far above what c-Si producers could achieve. Arguments that the CIGS modules produced more kilowatt-hours per kilowatt peak, particularly in times of lower direct irradiation or higher temperatures, couldn’t cut through the reality of higher costs on the factory floor.
In the face of these challenges, Solar Frontier had long traded on its strong sales channels in Japan, the undoubted quality of the modules themselves, and attempts to enter new market sub-segments. Like several CIGS providers before it, Solar Frontier developed specialised modules, small formats for the tight Japanese residential rooftops, and flexible modules for weight-constrained roofs, to carve out applications in which competition on price did not predominate.
However, a revealing decision by Solar Frontier was that it would deploy monocrystalline silicon in its new module series, announced in November. The company’s CIGS technology could not compete – and the technology joined a long list of thin-film contenders that had failed in the face of the impressive efficiency gains and cost reductions that had been achieved by predominantly Chinese c-Si rivals. With the same dimensions, the lighter Solar Frontier c-Si module hits a power output of 250 W, compared to 190 W in its CIGS predecessor.
BIPV contested
That building integrated photovoltaic (BIPV) applications should be the ideal fit for thin-film PV technology simply stands to reason. The monolithic nature of thin-film PV gives a uniform appearance over the glass surface, meeting the aesthetic requirements of architects. Black or blue crystalline silicon cells, even when spaced widely in the dual-glass facade, remain visible and are conspicuous, by contrast.
When it is also considered that thin-film semiconductors can be deposited onto flexible substrates – opening up curved surfaces and roofs unable to bear the weight of framed-glass modules – thin film becomes an obvious BIPV technology.
Organic PV (OPV) could also be produced in a dazzling array of colours, module formats and with semi-transparency, however the technology tended to deliver low conversion efficiencies – well below double digits.
Ideally in these applications the proponents of thin films would find opportunities. The price-per-watt factor was less important, meaning that the technology could compete. And when form factor, weight and even colour were considered, thin films were seen as having uncontested turf in BIPV applications. There was, it seemed, space in the solar world for all solar technologies.
However, increasingly it appears this is not the case.
C-Si alternatives
In 2021, there are an ever-growing number of c-Si module producers offering products for BIPV applications. From c-Si integrated solar tiles to coloured modules and specialised mounting structures, there is a wide array of crystalline silicon products that can be incorporated into the building structure itself. Major c-Si producers like JinkoSolar and Maxeon have paid increasing attention to BIPV applications, while more specialised producers like Hevel Solar and Mitrex produce BIPV products that offer architects a wide array of options to meet their demanding aesthetic needs.
“We are working with crystalline technology and it is advancing a lot,” says Teodosio del Caño, the CTO of Spain-based BIPV producer Onyx Solar, which produces bespoke thin film and c-Si BIPV modules. “We would say that today we are doing 70% crystalline and 30% amorphous silicon (a-Si).”
Del Caño explains that the company is using offline a-Si production equipment from a European producer as it delivers the flexibility to produce modules at a range of module dimensions. A-Si technology also allows Onyx to tailor the level of light that passes through the module – to allow for 10, 20 or 30% transparency. Onyx does this by etching strips of the a-Si semiconductor off the glass with its laser process, which would not be possible with CIGS due to the molybdenum (Mo) back layer – which is very tough and problematic to laser etch.
However, it’s the c-Si product range that is gaining significant market traction for Onyx, in a year that the company describes as “the best in our history.” Advances in lamination technology are allowing the company to produce c-Si modules of sufficient thicknesses to be deployed as safety glass for sound barriers, and with glass colours and textures that can completely mask the c-Si cells inside.
“We have a really prominent position in the market because of our lamination capabilities,” says del Caño. “Compared with the beginning of BIPV, it leads us to a position where the client chooses crystalline [PV] as the main, best solution for their projects.”
Inside lamination
There have been significant advances in glass lamination technology in recent years. Coating technologies allow increasingly advanced materials to be applied to architectural glass, delivering a range of thermal and even dynamic transparency capabilities.
For BIPV, the ability to laminate modules using thick glass is a particular challenge and a requirement for the safety glass required for certain building applications, up to 10 mm thick for the front and back glass for wind loads and other weather impacts. For German lamination equipment provider Bürkle, it presents an opportunity to apply the expertise developed in the safety glass lamination industry to PV.
“They [very thick glass sheets] are a challenge for conventional lamination as the membrane process is not ideally suitable for modules of this thickness,” explains Robert A. Gaiser, the sales director for PV and technical glass at Bürkle. “The corner pressure in lamination can create voids and the lifetime of the [laminator] membrane is dramatically reduced.” Gaiser says that as a result, Bürkle developed a new membrane-free process that the company predominantly deploys for architectural safety glass production but is also applicable to BIPV. “The process uses a vacuum flat press already in the first lamination step instead of a conventional membrane press,” Gaiser explains.
But it is perhaps in the addition of coloured or patterned coatings onto the glass or within glass that is facilitating c-Si technology’s challenging of thin films. If the c-Si cells can be masked and BIPV modules with a wide range of colours produced, architects and construction companies will be more willing to incorporate solar into their building designs.
Companies such as Hevel, Mitrex and Onyx are unwilling to release details as to how they produce the coloured or patterned glass for their modules. However, Gaiser says that foils or coatings are commonly used for BIPV applications, and that the experience of material applications such as anti-reflective coatings, now near-universal in PV, have allowed for equipment providers to develop reliable techniques for mass production. He says roller coating is the most common technique. “Of course, it is important to apply such coatings homogeneously, but our state-of-the-art technologies are already suitable for the most part for such coatings.”
With any coloured or patterned module coating there will always be a trade off with efficiency. However, with the a-Si used by producers such as Onyx achieving something like 8% conversion efficiency, c-Si producers, with 18% module efficiency seen as the low end in 2021, there is plenty of performance to play with. Russia’s Hevel, for example, is using 23.8% efficient heterojunction cells in its new BIPV line, meaning coloured coatings may diminish output but still leave impressive conversion efficiency.
Wide market
With the global solar market likely to exceed 160 GW in 2021, and mounting imperatives to decarbonise the built environment, there is a growing number of opportunities for agile manufacturers.
In Europe’s north, Midsummer is deploying its CIGS technology. Midsummer first entered the solar PV market as a CIGS production equipment supplier, but it has now pivoted to producing BIPV solar roofing modules alongside its tooling business. It initially supplied modules to its home Swedish market and is now looking to expand into southern Europe from a new 50 MW production facility in Italy.
Midsummer’s Wave product integrates its stainless-steel substrate CIGS cells into roofing tiles, in a way that delivers the same aesthetic as a solar tile or shingle, but without the abundance of cables and connectors that existing, similar products do. A single Wave module can be installed across five roof tiles and integrated into existing roofs – another differentiator from solar tile or shingle makers, which each have a bypass diode, junction box and two connectors for each tile. And with conversion efficiencies of 15-17%, the Midsummer Wave remains a high-performance product.
“I don’t know any kind of energy that can produce electricity with this low carbon dioxide footprint,” says Midsummer CEO Sven Lindström, speaking to an additional advantage of the company’s technology. “Midsummer solar panels come in at 6g/kWh [carbon footprint] in Sweden, and in Sydney or LA it’s between three and four [grams].” He adds that the carbon footprint has been verified by third parties.
Lindström says there is improved awareness of the importance of the carbon footprint of solar products from investors and for construction companies or building owners looking to integrate PV into their roof. The company also offers a more-conventional module for flat roofs.
From its entry into the PV production equipment market in the mid-2010s, Midsummer has been adept at identifying market opportunities and in the BIPV segment in southern Europe and Sweden, it believes there is ample opportunity for its CIGS technology in today’s PV marketplace. In contrast to 10 to 15 years ago, when fellow CIGS technology producers MiaSolé, Global Solar and Stion raised hundreds of millions in capital but could not achieve competitiveness, Lindström believes the marketplace is more mature and ready for the Midsummer thin-film offering.
“A lot of these thin-film companies, 10 to 12 years ago, were expanding too fast too early,” he says. “Maybe the technology was not mature. I see people looking at solar roofs in different ways today … The home is the most expensive thing many people will buy in their life. They will spend a lot of money on their house, and they don’t like the regular silicon panel aesthetics. And then the aspects on CO2 footprint, and that we’re not made in China, is creating a market which is really to our benefit right now.”
This content is protected by copyright and may not be reused. If you want to cooperate with us and would like to reuse some of our content, please contact: editors@pv-magazine.com.
2 comments
By submitting this form you agree to pv magazine using your data for the purposes of publishing your comment.
Your personal data will only be disclosed or otherwise transmitted to third parties for the purposes of spam filtering or if this is necessary for technical maintenance of the website. Any other transfer to third parties will not take place unless this is justified on the basis of applicable data protection regulations or if pv magazine is legally obliged to do so.
You may revoke this consent at any time with effect for the future, in which case your personal data will be deleted immediately. Otherwise, your data will be deleted if pv magazine has processed your request or the purpose of data storage is fulfilled.
Further information on data privacy can be found in our Data Protection Policy.