From pv magazine Global
Residential solar panels are often sold with long-term loans or leases, with homeowners entering contracts of 20 years or more. But how long do panels last, and how resilient are they?
Panel life depends on several factors, including climate, module type, and the racking system used, among others. While there isn’t a specific “end date” for a panel per se, loss of production over time often forces equipment retirements.
When deciding whether to keep your panel running 20-30 years in the future, or to look for an upgrade at that time, monitoring output levels is the best way to make an informed decision.
Degradation
The loss of output over time, called degradation, typically lands at about 0.5% each year, according to the National Renewable Energy Laboratory (NREL).
Manufacturers typically consider 25 to 30 years a point at which enough degradation has occurred where it may be time to consider replacing a panel. The industry standard for manufacturing warranties is 25 years on a solar module, said NREL.
Given the 0.5% benchmark annual degradation rate, a 20-year-old panel is capable of producing about 90% of its original capability.
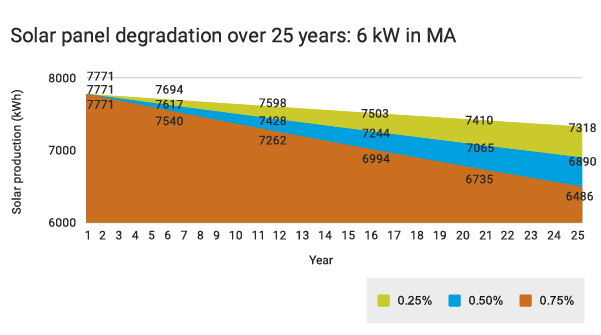
Panel quality can make some impact on degradation rates. NREL reports premium manufacturers like Panasonic and LG have rates of about 0.3% per year, while some brands degrade at rates as high as 0.80%. After 25 years, these premium panels could still produce 93% of their original output, and the higher-degradation example could produce 82.5%.
(Read: “Researchers assess degradation in PV systems older than 15 years“)
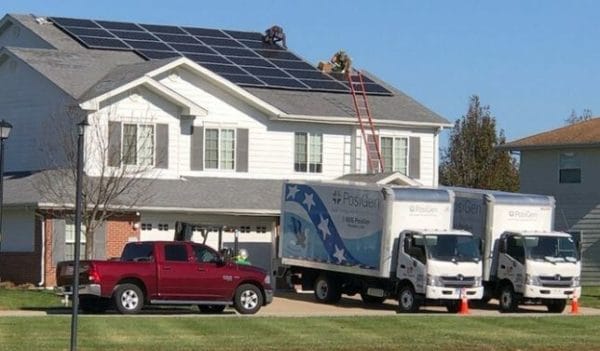
Some manufacturers build their panels with PID-resistant materials in their glass, encapsulation, and diffusion barriers.
All panels also suffer something called light induced degradation (LID), in which panels lose efficiency within the first hours of being exposed to the sun. LID varies from panel to panel based on the quality of the crystalline silicon wafers, but usually results in a one-time, 1-3% loss in efficiency, said testing laboratory PVEL, PV Evolution Labs.
Weathering
The exposure to weather conditions is the main driver in panel degradation. Heat is a key factor in both real-time panel performance and degradation over time. Ambient heat negatively affects the performance and efficiency of electrical components, according to NREL.
By checking the manufacturer’s data sheet, a panel’s temperature coefficient can be found, which will demonstrate the panel’s ability to perform in higher temperatures.
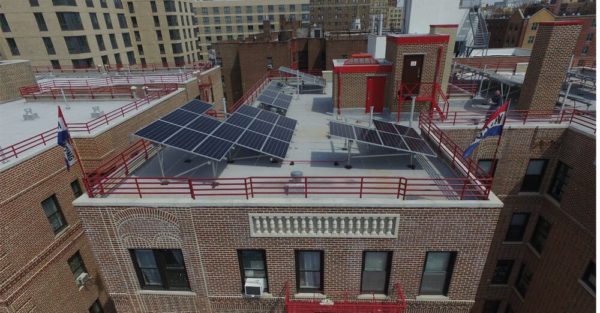
The coefficient explains how much real-time efficiency is lost by each degree of Celsius increased above the standard temperature of 25 degrees Celsius. For example, a temperature coefficient of -0.353% means that for every degree Celsius above 25, 0.353% of total production capability is lost.
Heat exchange drives panel degradation through a process called thermal cycling. When it is warm, materials expand, and when the temperature lowers, they contract. This movement slowly causes microcracks to form in the panel over time, lowering output.
In its annual Module Score Card study, PVEL analysed 36 operational solar projects in India, and found significant impacts from heat degradation. The average annual degradation of the projects landed at 1.47%, but arrays located in colder, mountainous regions degraded at nearly half that rate, at 0.7%.
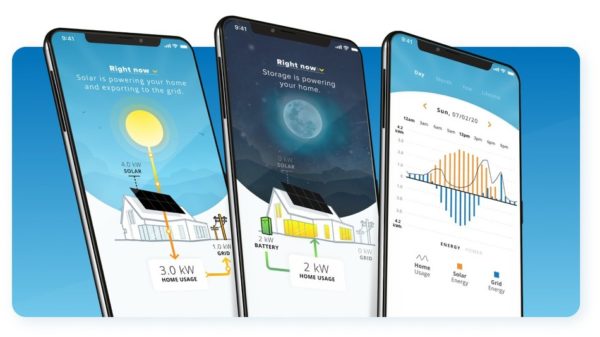
Proper installation can help deal with heat related issues. Panels should be installed a few inches above the roof, so that convective air can flow beneath and cool the equipment. Light-coloured materials can be used in panel construction to limit heat absorption. And components like inverters and combiners, whose performance is particularly sensitive to heat, should be located in shaded areas, suggested CED Greentech.
Wind is another weather condition that can cause some harm to solar panels. Strong wind can cause flexing of the panels, called dynamic mechanical load. This also causes microcracks in the panels, lowering output. Some racking solutions are optimised for high-wind areas, protecting the panels from strong uplift forces and limiting microcracking. Typically, the manufacturer’s datasheet will provide information on the max winds the panel is able to withstand.
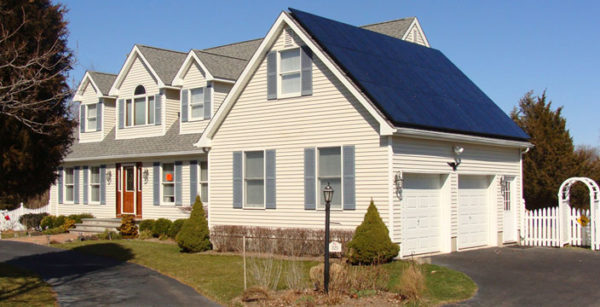
The same goes for snow, which can cover panels during heavier storms, limiting output. Snow can also cause a dynamic mechanical load, degrading the panels. Typically, snow will slide off of panels, as they are slick and run warm, but in some cases a homeowner may decide to clear the snow off the panels. This must be done carefully, as scratching the glass surface of the panel would make a negative impact on output.
(Read: “Tips for keeping your rooftop solar system humming over the long term“)
Degradation is a normal, unavoidable part of a panel’s life. Proper installation, careful snow clearing, and careful panel cleaning can help with output, but ultimately, a solar panel is a technology with no moving parts, requiring very little maintenance.
Standards
To ensure a given panel is likely to live a long life and operate as planned, it must undergo standards testing for certification. Panels are subject to the International Electrotechnical Commission (IEC) testing, which apply to both mono- and polycrystalline panels.
EnergySage said panels that achieve IEC 61215 standard are tested for electrical characteristics like wet leakage currents, and insulation resistance. They under go a mechanical load test for both wind and snow, and climate tests that check for weaknesses to hot spots, UV exposure, humidity-freeze, damp heat, hail impact, and other outdoor exposure.
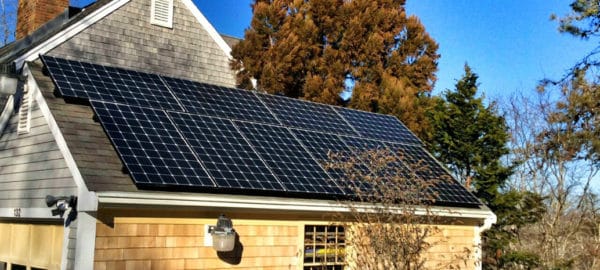
IEC 61215 also determines a panel’s performance metrics at standard test conditions, including temperature coefficient, open-circuit voltage, and maximum power output.
Also commonly seen on a panel spec sheet is the seal of Underwriters Laboratories (UL), which also provides standards and testing. UL runs climactic and ageing tests, as well as the full gamut of safety tests.
Failures
Solar panel failure happens at a low rate. NREL conducted a study of over 50,000 systems installed in the United States and 4,500 globally between the years of 2000 and 2015. The study found a median failure rate of 5 panels out of 10,000 annually.
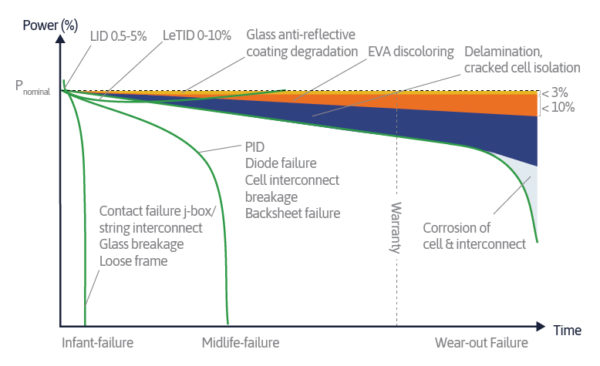
Panel failure has improved markedly over time, as it was found that system installed between 1980 and 2000 demonstrated a failure rate double the post-2000 group.
(Read: “Top solar panel brands in performance, reliability and quality“)
System downtime is rarely attributed to panel failure. In fact, a study by kWh Analytics found that 80% of all solar plant downtime is a result of failing inverters, the device that converts the panel’s DC current to usable AC. pv magazine will analyse inverter performance in the next installment of this series.
This content is protected by copyright and may not be reused. If you want to cooperate with us and would like to reuse some of our content, please contact: editors@pv-magazine.com.
By submitting this form you agree to pv magazine using your data for the purposes of publishing your comment.
Your personal data will only be disclosed or otherwise transmitted to third parties for the purposes of spam filtering or if this is necessary for technical maintenance of the website. Any other transfer to third parties will not take place unless this is justified on the basis of applicable data protection regulations or if pv magazine is legally obliged to do so.
You may revoke this consent at any time with effect for the future, in which case your personal data will be deleted immediately. Otherwise, your data will be deleted if pv magazine has processed your request or the purpose of data storage is fulfilled.
Further information on data privacy can be found in our Data Protection Policy.