A team of researchers from the University of New South Wales (UNSW) School of Photovoltaic and Renewable Energy Engineering (SPREE) has devised a reverse logistics model which they say leverages existing systems to improve the traceability of end-of-life solar PV modules and cut the costs associated with transporting them to recycling points.
Lead researcher David Leyton, a part of the research team overseen by Richard Corkish, chief operating officer of SPREE’s Australian Centre for Advanced Photovoltaics, and postdoctoral fellow Nathan Chang, detailed the Solar Reverse Logistics Model (SRLM) in a presentation at the Asia-Pacific Solar Research Conference in Sydney last week.
Leyton, a registered electrical contractor who is completing his PhD at UNSW, said the reverse logistics model relies on installers transporting end-of-life solar PV modules from the job site back to the warehouse from where they purchased the new modules.
The serial numbers of the end-of-life modules are recorded and allocated to a pallet or container which also bears a serial number. From there, the modules are ferried to a central collection point and onto a recycling facility.
“There are two aspects to the Solar Reverse Logistics Model; the serial numbers and the return leg of the electrician,” Leyton told pv magazine.
“The serial numbers are a no brainer. In the solar industry we are very sensitive to the serial number of the solar module. Every solar module that has ever been installed on the grid has been recorded and most importantly, the serial number has been recorded.
“We would use the same system to scan the serial numbers of the end-of-life modules and then add serial numbers to the pallets and containers along the logistics chain.
“You pick up modules, scan the serial numbers, take them to a container, scan the serial number of the container and then it is clear where those panels are. Then the container goes to a recycling facility, or it goes to reuse. It’s all manageable.”
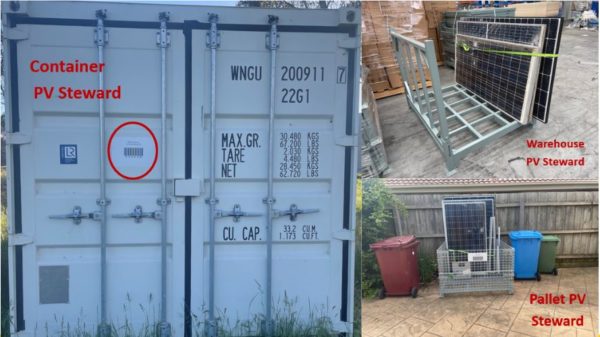
Image: UNSW
While tracking end-of-life solar PV modules might be a “no brainer”, overcoming the economic challenges associated with recycling solar PV modules has proved problematic. While solar PV modules are 100% recyclable, stripping and sorting the materials is a costly exercise and the return on those materials isn’t not yet large enough to cover those costs.
“The main problem with recycling solar modules is that at the end of their life they are not worth as much as they were at the beginning,” Leyton said. “When you recycle them, the value you get out a recycled solar module is the equivalent value of some aluminium and some glass and a little bit of silicone and silver. Plus, you have to spend an awful lot of time and energy deconstructing your module. That’s the challenge.”
Leyton said the SRLM approach would help cut costs on the logistics side, making recycling a more attractive proposition.
“With the installer transporting the used modules back to the collection point you eliminate the need for someone else to fulfil that role,” he said. “You don’t have two vehicles going out to the same site. The installer takes on another role and they get compensated for that role.”
The idea to utilise the installers to transport the used modules was discovered almost by chance. Leyton said while collecting modules from the warehouse for an installation, he noticed one of the panels was damaged. The panel was replaced but Leyton opted to take the damaged panel with him and while driving away the reverse logistics model became clear.
“When you deal with modules a lot, when you install them, deinstall them, move them, transport them and so on you get a different perspective,” Leyton said.
“The lightbulb moment happened when driving home with both the new modules and the one smashed module in the van.
“The same installer can take new modules to site and he or she can take the end-of-life modules back from site.”
“The electrician or the solar company or whoever is doing the job is coming to the property with new panels, therefore they have space to take the old panels away.”
While acknowledging the “details and the economics and who pays who and how much for each panel” is still to be resolved, Leyton said Australia’s embrace of solar means it is imperative strategies are put in place to ensure end-of-life modules are reused or recycled, reducing the amount of waste heading to landfills.
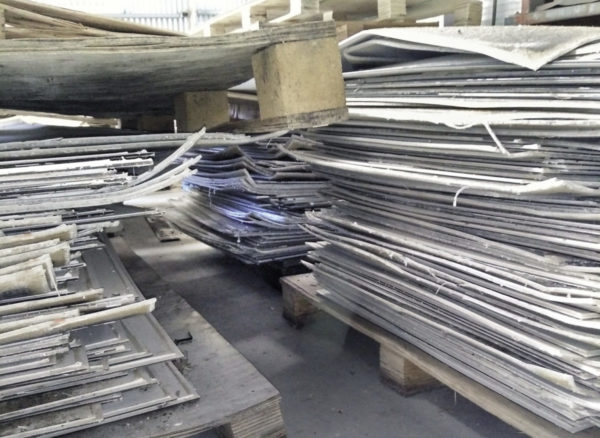
Image: LG
According to the nation’s Clean Energy Regulator (CER), as of mid 2021 there were more than 3 million residential, commercial, and large-scale solar PV installations across Australian with a combined capacity of more than 22.3 GW.
That uptake is generating what some have labelled a “landfill nightmare”. In 2018 Australians generated 2,700 tons of PV waste as the earliest modules reached their end of life. It is estimated more than 100,000 tons of modules will enter the national waste stream by 2035. By 2050, it’s expected there will be 1.5 million tons of solar PV waste in Australia.
“The industry is booming but the only problem with all this solar is that it has to be recycled. It has a finite lifespan,” Leyton said.
“My solution is we in the solar industry are responsible, not the couriers, not the waste people, not the customer, we are responsible.
“The installer should take back the solar module to a wholesaler or site that can receive them. If they take it back to a wholesaler it makes perfect sense. Wholesalers have space plus they are getting trucks coming to them with modules and they are leaving empty. It would make a whole lot more sense to take the end-of-life module back to the wholesaler and the wholesaler to put the end-of-life modules on the trucks which are delivering to them in the first place and then they go back to a central citywide hub. That’s the reverse logistics.”
Leyton said the SRLM concept has attracted support from the industry, including installers and manufacturers.
“There’s been a lot of industry interest,” he said. “I’ve spoken with a number of manufacturers and the evidence is that they are more than willing to bear their share of responsibility.
“I don’t think you’re going to get any resistance from anyone in this industry to a way forward.”
This content is protected by copyright and may not be reused. If you want to cooperate with us and would like to reuse some of our content, please contact: editors@pv-magazine.com.
By submitting this form you agree to pv magazine using your data for the purposes of publishing your comment.
Your personal data will only be disclosed or otherwise transmitted to third parties for the purposes of spam filtering or if this is necessary for technical maintenance of the website. Any other transfer to third parties will not take place unless this is justified on the basis of applicable data protection regulations or if pv magazine is legally obliged to do so.
You may revoke this consent at any time with effect for the future, in which case your personal data will be deleted immediately. Otherwise, your data will be deleted if pv magazine has processed your request or the purpose of data storage is fulfilled.
Further information on data privacy can be found in our Data Protection Policy.