In a fresh take on the solar car concept, a team of scientists from Sydney’s north will test printed organic photovoltaic panels by embarking on an 84-day journey around Australia.
The team plan to charge an electric Tesla vehicle (EV) by unrolling 18 flexible panels beside the car forming an off-grid charging system. The organic solar cells being deployed have been printed on laminated polyethylene terephthalate (PET) plastic by a printer formerly used for wine labels.
The 18 metre long ultralight and ultraflexible strips are similar in thickness and appearance to a chip packet, the university team have said. The project will see the technology’s performance and durability tested in the real world, while also offering the team an opportunity to educate along the way.
The Charge Around Australia project is set to embark in September and is a partnership between the UK company Charging Around Britain Ltd and the University of Newcastle’s Centre for Organic Electronics, where the printed solar cell technology was developed by Professor Paul Dastoor and his team.
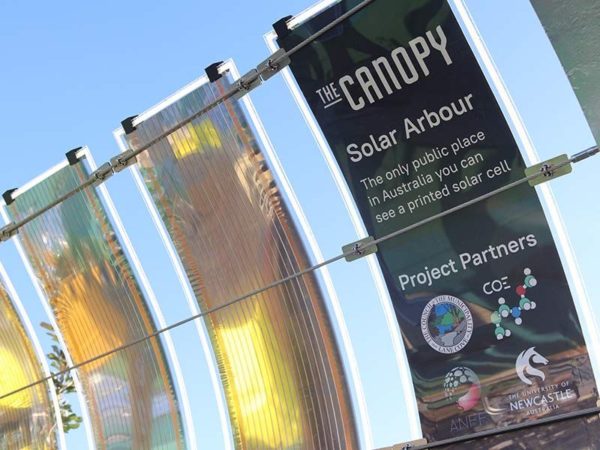
Lane Cove Council
“This is actually an ideal test bed to give us information about how we would go about using and powering technology in other remote locations, for example, in space,” Professor Dastoor told Reuters about the project.
The main challenges for printed organic photovoltaics are efficiency and durability, the Charge Around Australia project notes. It says extensive economic modelling has found that even with modest device efficiency and lifetimes, large area oriented solar technology can compete with coal generated power.
“The projected efficiency of a pilot scale installation is around 1%–2% with a lifetime of between one and two years,” the project’s website says, adding that for manufacture at scale, this would correspond to a cost of electricity as low as $0.88 per kWh.
The university teams says its technology can be manufactured at a production cost of less than $10 per square metre and can rapidly be produced, with commercial scale equipment capable of printing kilometres of material a day.
“No other renewal energy technology can be manufactured as quickly. The low cost and speed at which this technology can be deployed is exciting as we need to find solutions, and quickly,” Professor Dastoor said.
Over 99% of the panels are made from polyethylene terephthalate (PET) plastic, for which the Newcastle team is currently looking into recycling processes. “Our hope is that we can separate the outer PET layers and reuse them to make new panels with minimal processing,” Professor Dastoor said.
The technology has already been deployed in the form of a solar arbour in Sydney’s Lane Cove, which opened in June 2020.
The low-cost, lightweight, flexible solar technology could hold promise for a range of applications including disaster relief and recovery; retractable recharging systems for electric vehicles, caravans, camping and the defence industry; floating covers for dams and pools; yacht sails; smart blinds for residential and high-rise buildings; greenhouse covers and more, the Newcastle University team have said.
In the Charge Around Australia project, the team is aiming to dispel “range anxiety” around electric vehicles and prove how efficient solar technology can be at car charging. The project will also see scientists visit around 70 schools to teach students about renewable energy technologies and future potential.
This content is protected by copyright and may not be reused. If you want to cooperate with us and would like to reuse some of our content, please contact: editors@pv-magazine.com.
Can you install this o top of flat roof of 100X100 feet size to be used for energy supply of a lorge building?
Hi Dr Syan, that question is probably best directed to University of Newcastle’s Centre for Organic Electronics, though I would imagine commercial solar panels are probably preferable in that scenario.