Engineers at the University of New South Wales (UNSW) say they’ve built a high-speed motor that could extend the range of electric vehicles (EVs) by delivering a better power-to-weight ratio than existing technology.
A team, headed by Associate Professor Rukmi Dutta and Dr Guoyu Chu from the UNSW School of Electrical Engineering and Telecommunications, said the new technology improves upon existing interior permanent magnet synchronous motors (IPMSMs), which are predominantly used in traction drives for EVs.
The maximum power and speed achieved by the motor has doubled the existing high-speed record of laminated IPMSMs, notching speeds of 100,000 revolutions per minute, making it the world’s fastest IPMSM yet built with commercialised lamination materials.
The engineers said more significantly, the motor is able to produce a very high power density, which is beneficial for EVs in reducing overall weight and therefore increased range for any given charge.
“One of the trends for electric vehicles is for them to have motors which rotate at higher speeds,” Chu said. “Every EV manufacturer is trying to develop high-speed motors and the reason is that the nature of the law of physics then allows you to shrink the size of that machine. And with a smaller machine, it weighs less and consumes less energy and therefore that gives the vehicle a longer range.”
The engineers said the design of the new motor, inspired by the Gyopo rail bridge in South Korea, also overcomes a flaw common with traditional IPMSMs. An IPMSM type motor has magnets embedded within its rotors to create strong torque for an extended speed range. However, existing IPMSMs suffer from low mechanical strength due to thin iron bridges in their rotors, which limits their maximum speed.
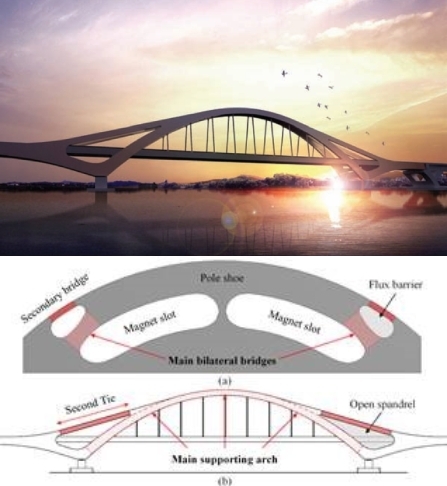
Image: UNSW
The UNSW Sydney team used a double-tied arch structure to design a new rotor topology and create a stronger version of the existing technology, delivering a better power to weight ratio.
“With this research project we have tried to achieve the absolute maximum speed, and we have recorded over 100,000 revolutions per minute and the peak power density is around 7 kW per kilogram,” Chu said.
“For an electric vehicle motor we would actually reduce the speed somewhat, but that also increases its power. We can scale and optimise to provide power and speed in a given range – for example, a 200 kW motor with a maximum speed of around 18,000 rpm that perfectly suits EV applications.”
The UNSW team said the new motor also offers a significant cost advantage over existing technology and uses less rare earth materials per unit.
“Most high-speed motors use a sleeve to strengthen the rotors and that sleeve is usually made of high-cost material such as titanium or carbon fibre,” Chu said. “Our rotors have very good mechanical robustness, so we don’t need that sleeve, which reduces the manufacturing cost. And we only use around 30% of rare earth materials, which includes a big reduction in the material cost.”
While the motor is still a prototype, Chu said it could be easily adapted to suit an individual EV manufacturer’s demands
“If an electric vehicle manufacturer, like Tesla, wanted to use this motor then I believe it would only take around six to 12 months to modify it based on their specifications,” he said.
This content is protected by copyright and may not be reused. If you want to cooperate with us and would like to reuse some of our content, please contact: editors@pv-magazine.com.
Very interesting article about electric motors.
Australia has the technology, the knowhow and experience (from when we had 3 car makers), and the raw materials, such as iron ore (to make steel) and lithium (for lithium-ion batteries) to give us the potential to be a world-leading manufacturer of electric vehicles.