Australian National University (ANU) spinoff Syenta has just completed a $3.7 million (USD 2.46 million) seed funding raise to help deliver its 3D electronics printers to early customers. After working on the technology for the last three years, co-founder and CEO Jekaterina Viktorova tells pv magazine Australia the startup will shortly be seeking feedback on its initial printer, which can be used to build electronic prototypes.
“We call it a printer for electronics but really its a multi-material additive manufacturing technology. You can literally make anything you want,” says Ben Wilkinson, Syenta’s head of research and development.
Syenta prints with electrochemistry, using a purely additive method. “We basically use electricity to deposit patterns of material,” Wilkinson explains.
Syenta prints with electrochemistry, using a purely additive method. This approach holds potential to reshape manufacturing costs due to simplicity, but also because the printer uses what are essentially precursor materials. That is, if someone wants to print with copper, the “ink” would actually be a copper ink. “Our method turns the raw material into copper as we’re printing it,” Wilkinson says.
“The other really exciting thing is that our process can work in reverse. So we [can] turn the [for instance] copper back into copper salt, and that just becomes new ink that we can reuse,” he adds. “It’s getting much closer to how biology does it – where every resource can be reused again and it’s fully circular.”
For CEO Viktorova that’s the beauty of electrochemistry, “It’s reversible and it’s highly efficient compared to other methods.”
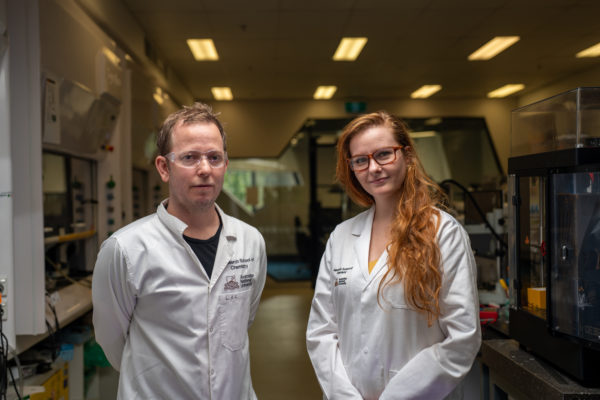
Image: Jamie Kidston/ANU
The approach strips away many of the process layers associated with traditional manufacturing, thereby reducing the amount of both energy and materials that go into producing electronics. It also liberates technologies from their supply chains, which in the renewables industry is looking increasingly valuable.
The other side of the proposition is what the additive manufacturing can offer to industries like photovoltaics, PCB, antennae, sensor and others. “For instance, we can make much more sophisticated designs faster and have complex geometries which improve performance of solar cells as well as reducing cost,” Wilkinson says.
“The geometry of those two technologies [solar and batteries] very strongly determines the performance. So how far physically do ions in batteries have to move to charge or discharge? Or, in solar cells, what is the resistance of electrons moving through the solar cell? If we can make that really, really small, on a nanoscale, we can dramatically reduce that resistance or time to charge.”
Potential applications aside, Syenta’s current printer – which is focused on enabling its customers to build technology prototypes – fits on a desk. “The next step is actually releasing the product,” Viktorova says. “We’re actually actively looking for people who are willing to prototype using our tech and have this inform our future full product building activity, which will be the product that ends up on our website and shipping worldwide.”
Eventually, the company’s ambition is to target large-scale electronics manufacturing. “We think we can do better at a lot of existing manufacturing steps for electronics,” Wilkinson says.
“The potential of our technology is really high in terms of how fast it can go but at the moment the way we do it is quite slow,” he adds. “It’s focussed on prototyping but we think we can do large scale manufacturing and the process is really suited to that but there’s just a lot of engineering that has to happen to build out that capability.”
To date, the vision of scalable additive manufacturing from 3D printing remains unfulfilled.
Syenta’s backstory
The core of Syenta’s tech started with a late night email between Viktorova and her then PhD supervisor – now co-founder – Professor Luke Connal. The next day in the ANU lab, Viktorova started to experiment.
While several academics had tried a similar approach before, Viktorova says no one had done it in quite the same way and, perhaps more importantly, her PhD meant she could dedicate years to refining and testing to get it right.
“The timing and combination of skills was just right for us to get it to the next commercialisation step,” she adds.
Syenta, which recently changed its name from Spark3D, is now separate from ANU, though close collaboration with the university and the research continues.
Additive printing based on electrochemistry
To explain how the startup’s approach works, Wilkinson points to the chrome hubcaps donned by fancy cars. That plating, he says, is a form of electrodeposition. “What we do differently is we don’t have to use chrome, we can use lots of different materials and also we print in a very small area. We can do complex patterns with this kind of plating of material.”
In terms of the “additive” component, this refers to an approach of only adding materials. This is different from most manufacturing processes, which both add and subtract materials.
“I think that’s a unique value proposition in itself,” Viktorova says, referring to the additive approach. “You don’t have as much literal waste.”
Syenta’s current printer prints with metals, alloys, conductive and insulating polymers and semiconductors.
The printer can do a single layer printed circuit “in minutes,” Viktorova says, “as opposed to other developed technologies spending hours doing that.”
Solar manufacturing potential
Wilkinson points to silicon solar cells and microchips as interesting ways to think through Syenta’s approach. Silicon microchips require high resolution, as in highly complex patterns on a small space, whereas silicon solar cells require far less detailing, making them “low res,” but are manufactured across far larger areas.
“The potential of our technology is to be able to do both of those things at same time – so have the nanoscale, resolution complexity at the speed and area of solar cells,” Wilkinson says.
Viktrova adds that the technology has “quite an interesting relationship between precision of fabrication and speed – it’s quite linear, which is a very unique thing to have. That’s why we believe there is a unique scalability even in our prototyping product that is intrinsic to the technology itself.”
Viktorova describes solar as a particularly interesting market for Syenta thanks to the similarity of set up; “They just use different technology [to manufacture] – usually additive in combination with subtractive. So we’re very keen to save this extra step for someone.”
Broader applications
Beyond solar, the 3D printer has a huge range of other manufacturing applications. “A lot of the designs that people currently make devices in are limited by the constraints of the current manufacturing landscape, or even prototyping landscape,” Viktorova says.
“Imagine you unleash that creativity and allow people to make something they could not make before because they did not have access to the right tool.”
Environmental impacts
Making more stuff generally translates to more pollution. But Wilkinson says using the emissions scope equation, the Scope 1 emissions from the printer are nothing – at ANU at least the printer runs on renewable electricity.
In terms of Scope 2, the printer’s additive approach means no more materials are used than absolutely necessary. What is deposited is deposited well and fast and in a way that makes it recyclable, meaning each finished, printed product has the least embodied energy it can for its output, he says.
As for Scope 3, Wilkinson notes the technology gives people the ability to make better, cheaper devices that can increase the uptake of renewable technology, whether it be batteries, solar, smart devices or ways to connect to the Internet of Things (IoT). “If that’s really cheap, more people adopt it,” Wilkinson says.
The reversibility component of the technology is particularly important for the startup. “We’re building towards being able to recycle whatever we print in the same product in the same system,” Viktorova says.
Climate Launchpad
In this year’s round of the global Climate Launchpad program, Syenta (then Spark3D) made the global semi-finals – the furthest any Australian startup has progressed. Its success in the competition secured Syenta a spot in the ClimateLaunchpad accelerator program, aimed at helping startups successfully commercialise into businesses.
Syenta will participate in the program in 2023.
Large-scale manufacturing
In terms of big picture vision, the Syenta team thinks their technology holds much promise for large-scale electronics manufacturing, with Wilkinson saying he believes the “bulk” of electronics manufacturing could be done better using its method.
Europe has a rich printed electronics manufacturing ecosystem, Viktorova says, and this is is something Syenta is hoping to delve into and learn from in the near term.
“We would like to make a product that sits in existing supply chains, or existing production lines that would be faster and cheaper and has this resolution patterning benefit,” Wilkinson says. “I’m sure it will happen, but it just takes time and effort to get that done.”
It will also require a fair amount of resources and financing, something not lost on the team. Building on the recent seed capital raising, Viktorova says the company will look to fundraise for the next commercialisation stages in the coming years.
This content is protected by copyright and may not be reused. If you want to cooperate with us and would like to reuse some of our content, please contact: editors@pv-magazine.com.
By submitting this form you agree to pv magazine using your data for the purposes of publishing your comment.
Your personal data will only be disclosed or otherwise transmitted to third parties for the purposes of spam filtering or if this is necessary for technical maintenance of the website. Any other transfer to third parties will not take place unless this is justified on the basis of applicable data protection regulations or if pv magazine is legally obliged to do so.
You may revoke this consent at any time with effect for the future, in which case your personal data will be deleted immediately. Otherwise, your data will be deleted if pv magazine has processed your request or the purpose of data storage is fulfilled.
Further information on data privacy can be found in our Data Protection Policy.