This month, Aurecon, an Australian engineering, design and advisory company, took out Gold in the ‘Digital – New Service or Application’ category at the Melbourne Design Awards, for siteLab, the data-agglomerating digital design and visualisation tool it has developed over several years to enable smarter, cost-effective decision making on engineering and infrastructure projects.
Aurecon’s Energy division works both publicly, and discreetly under the radar, on numerous renewable energy studies and projects. The 64 MW Warwick Solar Farm, for example, which announced completion on Friday, and contributes to UQ becoming the world’s first major university to offset 100% of its electricity use with renewable power produced from its own assets, found traction in an Aurecon pre-feasibility study. Aurecon subsequently advised on design, construction tendering and physical build of the asset, which will also be used by the University for research into technologies such as battery energy storage and hydrogen conversion.
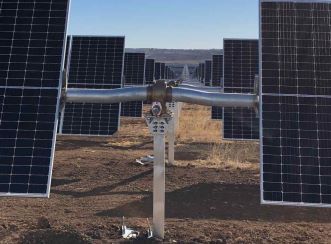
Image: Aurecon
Other Aurecon commissions include SA Water’s $300 million project to achieve zero-cost energy in powering its water and sewerage services by implementing energy efficiencies and increasing renewable energy generation and storage across its statewide sites; and a number of projects to help the South Australian Government achieve energy security as it integrates a record high penetration of renewables, including advising on project definition, procurement, execution and testing of the Hornsdale Power Reserve, and setting VPP-capable standards for behind-the-meter residential batteries approved for the South Australian Home Battery Scheme.
The company also provides grid modelling for the Australian Energy Market Operator (AEMO) and network service providers; and engineering and advisory services to major infrastructure investors, project developers and large energy consumers.
pv magazine talked to Dave Mackenzie, Managing Principal of Creative Technology & Visualisation at Aurecon, and Ben McGarry, the company’s Future Energy Capability Leader, about what siteLab digital smarts bring to renewables development, and the trends that Aurecon sees emerging in the solar, battery and grid-stabilisation areas.
pv magazine: Congratulations on receiving the design award for siteLab. What does the win mean to you, and what does this engineering software do?
Dave Mackenzie: It’s meant validation of the effort we’ve put into siteLab over the years and also validation of some of the outcomes from the projects where we’ve used siteLab.
The tool framework sits on top of game-engine technology, and has virtual reality as a standard feature. Basically, our framework enables the stack of design optioneering on data flowing in and out of the application. Gone are the 2D drawings, foam models and unresponsive 3D renders of the past. By introducing a single visual language, siteLab brings all stakeholders together on the one online platform, to view engineering progress and tackle challenges as they arise.
Creating digital twins of complex systems can detect deviations from normal operations and allow predictive maintenance. Are you applying this technology through siteLab to large-scale renewable projects?
Ben McGarry: It’s not always clear what that term means. The value of a digital twin often comes in after design and construction on more established infrastructure, where it refers to synthesising and pulling together all sorts of data that wasn’t already in the same dataset: say, overlaying different spatial sets of data with plant data that might previously have sat in completely different places in a business.
For large-scale solar, we use very detailed digital modelling at the design stage; that is, all the work we do is effectively built from the bottom up so that you just have one repository of project data. It’s already a digital twin.
Can you give me an example of how Aurecon’s digital approach has improved the outcomes for a solar installation or a major battery installation on the NEM?
BM: I can give you a general sense of our process. First we combine the physical layout of the site with overall yield modelling and begin optimising the project’s design. In optimising the yield and performance on the DC side, we spend a lot of time on different module configurations: What are the panel layouts? What’s the row spacing? At the same time, we’re looking at the overall levelised cost of production for the project and balancing the yield with construction and O&M costs. That gives us a levelised cost model from the beginning. And as we’re playing with site layout, we can look at how that affects the project economics.
Getting into particulars of the design, you’re optimising things like cable routing, and constructability: What’s the cost of pre-assembling cable runs and terminal boxes and that kind of stuff off site? Then what’s the fastest and safest way to construct it once you’re on site? Lastly, once the design’s locked in and we’re looking at construction, we can use digital tools to track progress and optimise construction phasing. If, for example, the modules are delayed, or other components are delayed, or civils are slowed down because there’s some geotech issue, we can redo construction optimisation to account for that and minimise the impacts to the project.
Do you come in before developers take the model to investors?
BM: Some of the most sophisticated tools we’re working on are prospecting or project screening tools, and that’s really about modelling grid behaviours. Five years ago, solar development was all about finding the best resource. These days, it’s all about grid constraints, and congestion, system strength and curtailment. So we’re often working with the developer to understand even where a project should be, finding latent capacity in the grid, because there’s not much anywhere. In fact, there are huge swathes of the grid, particularly in New South Wales, where the existing capacity is massively oversubscribed with new renewable projects in the pipeline. So a lot of the time we’re helping developers understand where a project can be built and get its generation away at all. That’s well in advance of taking an investment thesis to an investor.
What trends are emerging as ways of optimising projects with great generation potential and a good chance of connection?
BM: Bi-facial modules are a really strong trend as developers look to maximise efficiency and minimise levelised costs.
Panel sizes are also progressively increasing; you’re looking at maybe 10-15% increase in size per annum, so 500-watt panels will soon be the norm. And that plays out when you look at the economics. The idea of jamming as much power as you can into a single module because installation cost is so high really favours increasing module size.
Behind-the-meter batteries are also becoming increasingly important. Sometimes that’s legislated or mandated, but often they’re included as a bit of a risk mitigation against curtailment. Lots of feasibility studies are going ahead with even a relatively small battery included, and that’s partly because developers are interested in understanding how they can make use of battery assets, partly a result of having seen the successes of the Hornsdale Power Reserve.
Tell us more about bi-facial technology. A couple of solar farms are deploying them. What’s holding bi-facials back?
BM: I think in Australia there just hadn’t been a major project to take the plunge and make use of them. Bifacials have only been around a few years in the mainstream. And then because construction doesn’t happen overnight, it’s sort of taken a while for that to work its way through. We’re working on a high-profile project that uses bi-facial modules and now we’re seeing a lot of the big solar farms proposing them. In fact, it’s become rare for us not to be working on projects that are planning to apply this technology. As I mentioned earlier, developers are looking to jam more yield into every single installed module. With bi-facials collecting light from the back of the panel as well as from the front, you’re boosting yield by up to 5% without having to change much else. You might need to increase the row size a bit, to increase performance of that reflected light to the rear of the modules, and you’re also refining the way the cables are reticulated on the underside of the panel, to minimise shading.
The other interesting thing is that once you get through the commissioning and you’re performance testing, the performance-test protocols don’t yet accommodate bi-facials, so you sort of have to negotiate how to test their performance. You have to factor in things like how reflective the ground surface is, in trying to measure the performance of the cell. It complicates the issue because it introduces a new source of uncertainty in the performance test, and you have to accommodate that in some way, whether it’s by changing the targets for the performance, or maybe working between the parties to land on a reasonable engineering view on how to take that measurement.
This content is protected by copyright and may not be reused. If you want to cooperate with us and would like to reuse some of our content, please contact: editors@pv-magazine.com.
1 comment
By submitting this form you agree to pv magazine using your data for the purposes of publishing your comment.
Your personal data will only be disclosed or otherwise transmitted to third parties for the purposes of spam filtering or if this is necessary for technical maintenance of the website. Any other transfer to third parties will not take place unless this is justified on the basis of applicable data protection regulations or if pv magazine is legally obliged to do so.
You may revoke this consent at any time with effect for the future, in which case your personal data will be deleted immediately. Otherwise, your data will be deleted if pv magazine has processed your request or the purpose of data storage is fulfilled.
Further information on data privacy can be found in our Data Protection Policy.