From pv magazine India
pv magazine: What are the challenges to battery energy storage manufacturing in India?
Nitin Gupta: The Prime Minister of India has set an ambitious target of 500 GW of non-fossil fuel-based energy generation in India by 2030 and a reduction of one billion tonnes in total projected carbon emissions by 2030. To meet these targets, India will need to ramp up its grid storage and significantly increase the number of electric vehicles (EVs). This, however, necessitates increasing local manufacturing, exploring new avenues, and allowing global competition in emerging sectors such as energy storage.
The production-linked incentive scheme for advanced-chemistry battery cells (PLI-ACC Scheme) permits a technology-agnostic approach. It allows the beneficiary firm to select any suitably advanced technology, the corresponding plant and machinery, raw materials, and other intermediate goods to establish a cell manufacturing facility to cater to any application.
The programme envisions an investment that will boost domestic manufacturing while also facilitating the creation of battery storage demand for electric vehicles and stationary storage and the development of a complete domestic supply chain and foreign direct investment in the country.
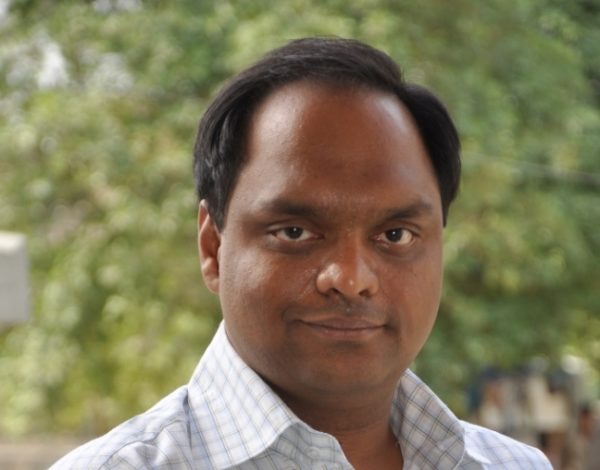
Attero
While the plan has its heart in the right place, a few things still need to be fine-tuned. The timelines for localisation appear to be too stringent, considering the lack of requisite manufacturing infrastructure and export base in the country. Incentives under the PLI-ACC Scheme will be disbursed only after the committed domestic value addition and actual sale of the ACCs. The bid documents call for a quarterly subsidy disbursement for the beneficiary company and certification from an independent engineer. The extent of the subsidy will vary depending on the engineer’s approval, affecting the practical implementation and timeliness of such disbursement. Furthermore, the above-mentioned subsidy limit will have to be considered when disbursing the subsidies.
The PLI-ACC Scheme provides that the beneficiary must achieve a domestic value addition of at least 25% and incur the mandatory investment (INR 225 crore/GWh) within two years. A penalty is levied every day beyond the timelines set for such localisation.
pv magazine: What India must do to address supply chain concerns?
China controls more than 97% of the world’s lithium supply even though it does not have any significant lithium mines. It created a refining infrastructure for lithium and became a dominant player globally.
India should take the lead in becoming the Li-ion battery recycling hub of the world. To do so, we have to ensure that we recycle all the Li-ion batteries in an environment-friendly manner. We also need to ensure maximum recovery of battery materials like cobalt, lithium, nickel, graphite, manganese, and copper. Both of these can be ensured by having the right recycling technologies in place, which is where Attero is right now.
India is already taking steps in this direction and is on the path of becoming ‘Atamnirbhar.’ We as a country also realise that recycling will play an important part in making us self-reliant. On the policy front, there have been a lot of initiatives taken in the recent past, and we should start seeing results soon.
pv magazine: What’s the current recovery rate in battery recycling at the global level, and what has been the target? What are the main concerns within the battery recycling process itself?
The global recycling industry is growing at a CAGR of 19.6% and is expected to reach US$22.8 billion by 2030, up from US$4.6 billion today. The extraction efficiency of Attero Recycling’s process is greater than 98% for all battery materials (cobalt, lithium, graphite, nickel, and manganese).*
pv magazine: Does India have the right policies and schemes to ensure a circular economy for batteries?
The government has been taking steps to promote a circular economy and encourage the concept of recycling. The government is also in the process of introducing extended producer responsibility (EPR) for Li-ion batteries. Under this, manufacturers will become accountable for the entire lifecycle of Li-ion batteries. Steps are also being taken to pump in more investments in the space.
Recycling is the best way to ensure our country’s long-term development. Metals account for more than 30% of a li-Ion battery in value terms. We do not have cobalt or lithium reserves in India. We can help India become ‘Atamnirbhar’ in these critical battery materials by recycling the end-of-life batteries. As India continues to leapfrog and prepare for the EV era, lithium-ion battery waste is expected to increase by 40-80%year on year. To brace for this revolution, we should also start preparing to manage and recycle the lithium-ion waste that these cars will produce.
–
Author: Uma Gupta
*This article was amended on April 27 to remove inaccurate statements.
This content is protected by copyright and may not be reused. If you want to cooperate with us and would like to reuse some of our content, please contact: editors@pv-magazine.com.
“while the next best process globally has an efficiency of only 50%.” & “Globally, no one is recovering pure graphite or any significant amount of lithium from end-of-life Li-ion batteries apart from Attero.”
I don’t know from where you get your data from? Is this just cheap marketing or has the interviewee living in a cave the past 2 years? It would be great if statements like these are vetted a bit more.
Hi Pete, noted. This transcript style of article meant these statements didn’t come under the same scrutiny – I will get in touch with our interviewer and bring it to attention. Cheers!