Lithium exists in one of those uncomfortable paradoxes where the act of getting the material needed for sustainability itself poorly impacts the environment. This is a rather unfortunate truth and one which industry generally prefer to overlook, at least when there aren’t many alternatives.
Vulcan Energy Resources, listed on the Australian stock exchange (ASX), however, believes it has found just that alternative – a method which has minimal environmental disruption and leaves behind infrastructure for ongoing renewable heating.
“We basically designed this process with existing technologies, but we were careful to exclude fossil fuels,” the company’s managing director and cofounder Francis Wedin told pv magazine Australia.
A geologist who initially worked in Australia’s gold mining sector before becoming intrigued by lithium in 2014, Wedin’s years spent examining ways to get the material using geothermal resources are now coming to fruition.

The company he cofounded with geothermal expert Horst Kreuter, based in Germany, has been running its pilot plant for over a year now and is currently building its demonstration plant, which Wedin says will mimic the scope of the real life project it is pursuing in Germany’s Upper Rhine region. “So there’s a lithium extraction demonstration plant and there’s the lithium processing to produce the end product,” Wedin says.
Despite being early days, Vulcan has already attracted not only Stellantis, with which it has a large offtake agreement extending to 2035, but LG Energy Solution, Volkswagen, Reno, and Belgian battery cathode specialist Umicore, all of which have secured offtake agreements for Vulcan’s future output.
In short, interest in Vulcan’s lithium is already well oversubscribed, much like its capital raises.
How Vulcan’s ‘zero carbon’ lithium extraction method works
Precisely what goes into getting battery minerals out of the ground can make people a little skittish. It often isn’t pretty, so we tend to instead focus on the technologies those products will go on to produce.
The lithium we use today largely come from two main sources: hard rock mining and brines. Australia is home to much of this hard rock mining, a high energy (and therefore high carbon footprint) process which pollutes its sites. The other option, mostly done in what’s known as the ‘lithium triangle’ in South America, involves evaporating lithium-rich brines. This is water intensive and usually uses polluting regents and gas for heating.
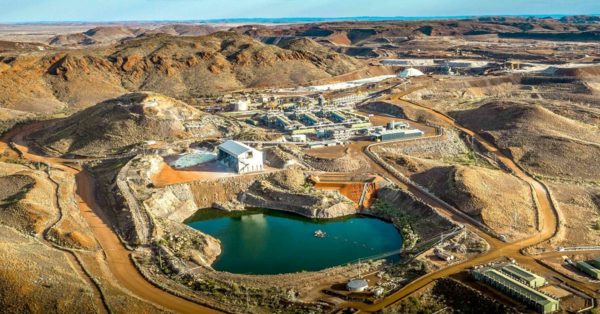
Image: Mineral Resources Limited / Twitter
Vulcan’s process also involves brines, albeit in a different way. Its process has three main components, the first of which involves pretty stock standard geothermal plants. Geothermal plants are longstanding and commonplace around the world, providing significant amounts of energy in places like Indonesia and some parts of the US.
Where geothermal is used depends on where reservoirs of hot fluid below the earth’s surface can be found. Basically generating geothermal energy involves drilling down into this hot liquid and using it heat up a secondary fluid, the steam from which drives a turbine which creates electricity.
“You can also, and this is increasingly what we’re planning to do… use it for heating as opposed to power,” Wedin says, noting using the resources specifically for heating rather than electricity incurs less conversion losses, making it more efficient.
One of Europe’s greatest geothermal resources is found in the Upper Rhine, which sits across the south west of Germany and into France. This is what Vulcan wants to tap into, not just because Wedin believes heating is “the elephant in the room in terms of decarbonisation,” but also because the fluid found in the Upper Rhine is very lithium rich.

Vulcan Energy Resources
Vulcan is already operating a geothermal plant in the Upper Rhine, and in April signed a contract to supply up to 350 GWh of energy per year to the city of Mannheim, in Germany’s southwest.
It’s envisioned future, though, will see it extract the lithium from the “hot, briny, lithium-rich fluid” before reinjecting it back into the Rhine in (crucially) a closed loop system.
“In this case, we divert the brine first through what we call an absorption plant and there the brine runs through a series of tanks,” Wedin explains. “The tanks are loaded with a type of absorbent. A bit like what’s used in water treatment, it’s an alumina-based resin. Basically, there’s lithium chloride within the brine and the lithium chloride adsorbs onto the resin. So it’s a Physicochemical process, it needs heat to work and the brine needs to be about 60 to 80 degrees.”
In the Upper Rhine, the brine “comes preheated,” as Wedin says. “That’s kind of advantage one.”
Pure water is then used to strip the resin of the lithium and reverse osmosis used to evaporate the excess water. “We use some of the steam from the geothermal plant to drive a forced evaporation process,” Wedin says. “So that’s advantage two.”
After all that, Vulcan is left with a lithium chloride concentrate which gets sent to a chemical plant. Importantly, the one Vulcan intends to use is situated just outside of Frankfurt, less than 100 kilometres away – a significantly shorter distance for processing than, say, Australia to China – the more usual route.
Lithium electrolysis
Wedin is eager to emphasise that Vulcan has focused on using existing methods and technologies for its processes, but notes that while all the components so far are commercially used already, the final step of lithium electrolysis is more novel.
“Lithium electrolysis not currently used commercially, but it’s very similar to the chloralkali industry,” he says. Essentially the company will use electrolysis cells, pretty much the same cells used by the chloralkali industry, to create the final lithium hydroxide product.
Vulcan has chosen this method over the more traditional reagent process because it has both a lower carbon footprint and reduces its costs. “We wanted to use electrolysis because we can use green power, green electricity,” Wedin says.
Project growth
Because of the structure of Vulcan’s process, its project is not one massive entity, but rather involves building a series of geothermal plants which will feed into the nearby chemical plant.
“So we’re able to grow in quite a modular fashion,” Wedin says. That is, the more plants it builds, the more it will increase its lithium output, giving it the capacity to scale with industry growth.
The fact that the Upper Rhine isn’t a single destination but rather a region which stretches deep underground (the wells Vulcan will drill are roughly between 2.5 to 5 kilometres deep) also means the plants can built anywhere within a wide radius.
“We don’t have to destroy any nature,” Wedin says, noting the plants could, for instance, be planned in former industrial areas or other locations where local communities see fit.
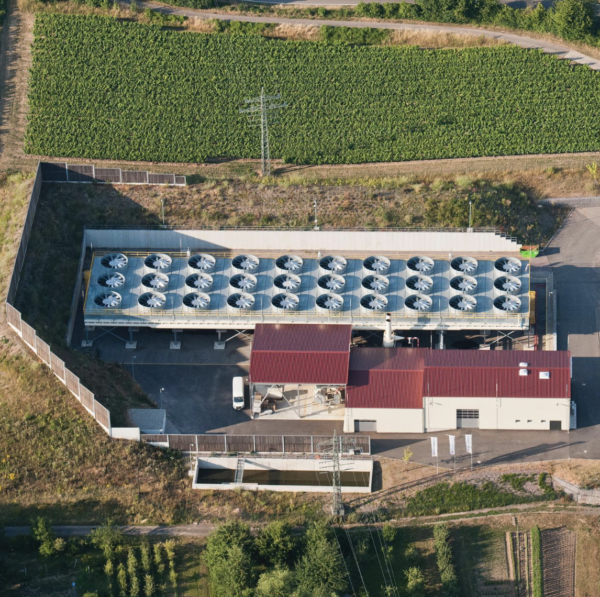
Image: Vulcan Energy Resources
In 50 years, when there is enough lithium in the system for it to simply be recycled, Wedin adds the infrastructure left behind by Vulcan’s endeavours can continue being used for ongoing heating and electricity in the local area. “So it fits in with a circular economy ideal.”
While the line Vulcan is selling its lithium on is ‘zero carbon lithium,’ Wedin thinks the process goes further than that. “We’ve designed it so we have a net negative carbon footprint because we’re exporting energy to the grid and displacing fossil fuels.”
Localising supply chains
In terms of what happens to the lithium, Wedin says the company’s idea was always to sell to either European-based businesses or companies with a specific focus on the region.
“We see markets as being much more localised in future,” he says, noting that geographically long supply chains have questionable relevance in a sustainable world.
Stellantis will be the project’s largest offtaker, and it is also the company’s second largest shareholder now. The $76 million (USD 47.8 million) of equity capital it invected into Vulcan this week will go towards to developing the drilling sites of the project.
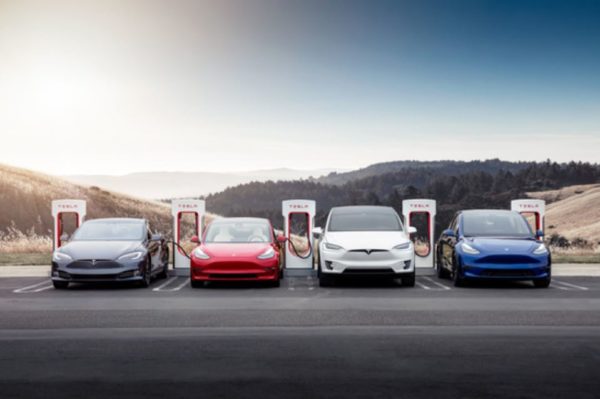
Image: Tesla
Next steps
In terms of what’s next for Vulcan, Wedin said the company is “going as quickly as possible.”
It’s currently working on its definitive feasibility study, also known as the bankable feasibility study. This is especially crucial for the project because while it is operationally forecast to be in the lowest cost quartile, Wedin says, “to get to that point, we need a large amount of capital.”
“So it’s high CAPEX, low OPEX basically.”
The roaring interest in offtake has definitely helped its financing prospects though, and Wedin says Vulcan is now seeking to expand its output. Its pre-feasibility study forecast a lithium hydroxide output of 40,000 tonnes, but in the feasibility study that number has been upped – though he wouldn’t say exactly how far.
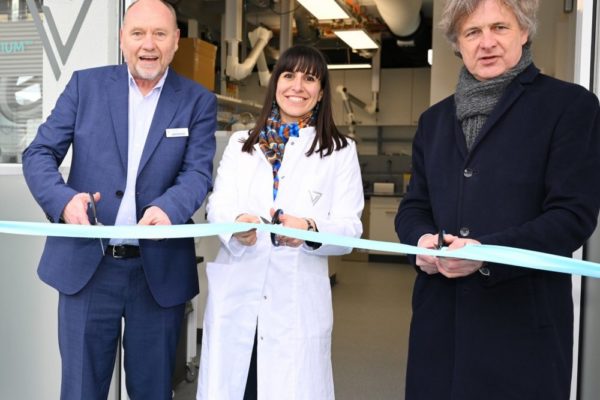
Vulcan Energy Resources
The company is also continuing to deepen its “strategic alliances” across the supply chain “because this is a big complex infrastructure project.”
“Stellantis was one, we are speaking to others,” Wedin adds, saying automakers, chemical companies and energy companies are all in the mix.
Vulcan’s demonstration plant is expected to be coming online towards the end of the year, with the lithium extraction component set for Q4, while the lithium electrolysis facilities should be commissioned by Q1, 2023.
The company today has 130 employees, many of which have been gained from strategic acquisitions of geothermal and other lithium companies. Of those, Wedin estimates 95% are based in Germany.
This content is protected by copyright and may not be reused. If you want to cooperate with us and would like to reuse some of our content, please contact: editors@pv-magazine.com.
1 comment
By submitting this form you agree to pv magazine using your data for the purposes of publishing your comment.
Your personal data will only be disclosed or otherwise transmitted to third parties for the purposes of spam filtering or if this is necessary for technical maintenance of the website. Any other transfer to third parties will not take place unless this is justified on the basis of applicable data protection regulations or if pv magazine is legally obliged to do so.
You may revoke this consent at any time with effect for the future, in which case your personal data will be deleted immediately. Otherwise, your data will be deleted if pv magazine has processed your request or the purpose of data storage is fulfilled.
Further information on data privacy can be found in our Data Protection Policy.