Just how a gold mining company born in the red dust of Western Australia came to be courting European carmakers with high purity, sustainably recovered battery materials has received surprisingly little airtime in clean energy circles, especially given the intrigue the company’s stock exchange listing alludes to. Repurposing technologies invented by mining, fostering European partnerships and amassing a series of striking core projects, Neometals has quietly reinvented itself, dislodging its foothold from regional backwaters and marching it directly into a global battery epicentre.
Just in the last week, Neometals completed the commissioning of its Primobius battery recycling demonstration plant. Located in its partner SMS Group’s manufacturing hub in Hilchenbach, Germany, an hour a half’s drive from former West German capital, Bonn, the facility uses distinctive hydrometallurgy processes to recover materials from lithium-based batteries.
What distinguishes the process though is its waste-free status. “We’ve developed flowsheets that not only try to maximise our recoveries, but that are actually green,” Chris Reed, Neometal’s managing director, told pv magazine Australia. “There’s no emission of any water, any waste water – we’ll be reusing that, and our tails are a fertiliser product and our CO2 footprint is very low.”
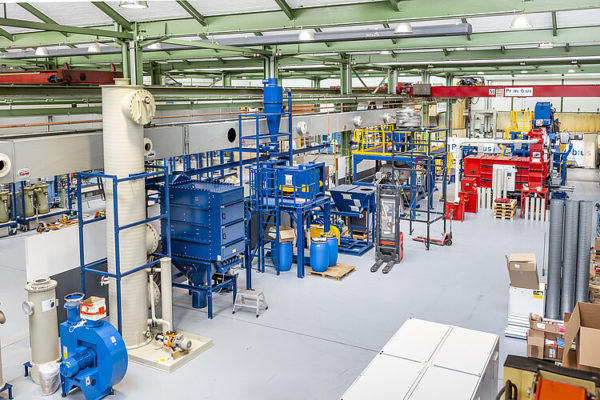
Primobius (Neometals & SMS Group)
The facility has been six years in the making, the result of an extensive research and development program by Neometals. After cracking the chemistry code, the company knew the real trick would be in scaling.
As Neometal’s general manager of commercial and investor relations, Jeremy McManus, puts it: European carmakers don’t have time for small Australian companies who are just going to build “one dinky plant”. Which meant Neometals had to find a way to go “very industrial scale” with its capacity or risk carmakers taking their battery recycling programs in-house. That capacity came in the form of the SMS Group partnership. To the joint venture, SMS Group brings its 140 year reputation in plant building, operation, maintenance, and permit know-how.
Attaching itself to an enduring European company has been vital for the Western Australian outfit. Neometals’ longterm strategy is to link with European carmakers by promising to close their car battery loop, recovering materials from their stocks of spent electric vehicle (EV) batteries so they can go into the next generation afresh – a ESG reporting dream. “That’s how we make money – it’s sort of a partnership model at large, where we manipulate sharing the economics, recycling services and selling the chemicals at the back,” McManus told pv magazine Australia.
The technology
Primobius uses solvent extraction as its primary recovery tool, a process Reed says was actually invented in the Australian mining hub of Mount Isa in central Queensland. “We’re still recovering nickel, cobalt, manganese, base metals, but instead of using a mineral source, we’re using the batteries,” Reed said. “It’s applying existing Australian technology into a new field.”
The Primobius pilot which took place in Canada saw materials recovery rates sitting around 85%, something Reed is hoping to boost in the more advanced German demonstration plant.
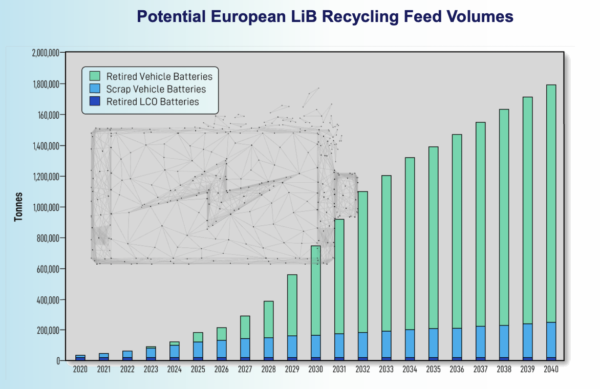
Neometals
A combination of Primobius’ sequence and reagents mean its process produces minimal waste. “Rather than using sodium as the pH adjustor, we used [the more expensive] ammonia gas which means instead of having a shitty sodium sulphate… we get ammonium [sulphate] out the backend, and it’s actually a very high purity fertiliser,” Reed explained. As for the gas fumes which come with battery recycling, Reed says the company actually captures its vapours, dries and condenses them “because that’s still got lithium in it.”
“Pretty much nothing goes to waste, or down the drain or into landfill,” McManus said of the process.
“We’re trying to design it as if you were going to build it next to your house [because] it’s going to be next door to someone somewhere in the world,” Reed said. This approach has seen Primobius selected as a finalist in the German Sustainability Award’s resources category for 2022, with the winner to be announced in early December.
The backstory
Neometals’ journey from gold mining in the turn of the century to (hopefully) winning sustainability awards in 2021 came, as Reed puts it, after “God slapped me in the face.”
It was Reed’s birthday, 2008, and he was watching concentrates being leached at Thyssenkrupp’s headquarters in Essen, Germany, when a cohort of engineers and businessmen emerged and told the Australian mining director that he should go looking for lithium. “They told me the future of transportation was going to be lithium batteries,” Reed recalled. Intrigued, he began researching.
As it turned out, Reed did know where to find lithium – there was a vast deposit right in his home state. He spent the next year shifting his business, which at the time was called Reed Resources, away from gold and toward lithium, eventually changing the company’s name to Neometals and extending the scope from just lithium to a broad spectrum of battery minerals.
“We [then] made a conscious pivot five years ago to move into those more sustainable materials recovery projects,” Reed said, pointing to the company’s turning away from its mining roots towards recycling.
The future
Primobius’ plan is to focus in on car batteries, specifically pursuing chemistries with high nickel contents, like lithium-nickel-manganese-cobalt or NMC chemistries and lithium-cobalt or LCO chemistries. Despite the surging popularity of lithium-iron-phosphate or LFP chemistries, the company isn’t prioritising that direction, describing it as far less economic. “You might get a cheaper car at the front end, but the the total cost is more expensive if you include recycling, which is where the world is going,” McManus said.

Primobius (Neometals & SMS Group)
It’s riding on carmakers, especially German luxury carmakers, opting away from cheaper, less flexible chemistries and towards more recyclable options. “All of my big discussions with potential partners, often the first person that ever speaks is the guy or girl responsible for lifecycle carbon analysis. Which Aussies don’t get, and I must admit I was a bit surprised,” McManus said.
For the Neometals team, Europe’s closed loop battery focus – not to mention incoming regulations – are leagues ahead of Australia. In the EU, battery makers will soon be mandated to use recycled content in their new products. “You can’t magic recycled content, it has to come from a recycler,” McManus said, opening up a seizable opportunity for well positioned players like Primobius.
“We’re doing a study on a 20,000 tonne per annum plant, and at the same time we’re doing a study on a 200,000 tonne per annum plant because that’s where we see the volumes going to,” he said.
Reed’s vision for Primobius is for it to become a preeminent global battery recycler. From his perspective, Europe is going to be where that first kicks off in earnest. “We’ll come to Australia as soon as the market is there,” Reed added.
Over this month, November, Primobius will complete the testing of its Hilchenbach demonstration plant and put the final touches on its feasibility study. It’s set to make its final investment decision on the endeavour in the first quarter of next year.
This content is protected by copyright and may not be reused. If you want to cooperate with us and would like to reuse some of our content, please contact: editors@pv-magazine.com.
By submitting this form you agree to pv magazine using your data for the purposes of publishing your comment.
Your personal data will only be disclosed or otherwise transmitted to third parties for the purposes of spam filtering or if this is necessary for technical maintenance of the website. Any other transfer to third parties will not take place unless this is justified on the basis of applicable data protection regulations or if pv magazine is legally obliged to do so.
You may revoke this consent at any time with effect for the future, in which case your personal data will be deleted immediately. Otherwise, your data will be deleted if pv magazine has processed your request or the purpose of data storage is fulfilled.
Further information on data privacy can be found in our Data Protection Policy.